
design parameters conveyordesign parameters for a ball grinding mill
مسكن > design parameters conveyordesign parameters for a ball grinding mill
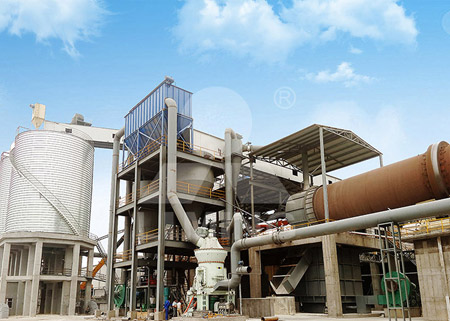

design parameters conveyordesign parameters for a ball grinding mill

Comparative Study on Improving the Ball Mill Process
In this study, the major process parameters tested are ball mill working capacity, ball mill speed and balls to powder weight ratio Planning of experiments was In our continuing effort to apply population balance models for scaleup and design of large diameter mills, a design method that combined the kinetic scale up Design considerations for large diameter ball mills ScienceDirect
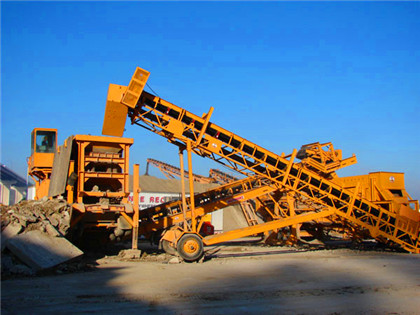
Grinding in Ball Mills: Modeling and Process Control
PDF The paper presents an overview of the current methodology and practice in modeling and control of the grinding Effects of ball mill types, feed sizes and ball surface area on particle morphology have been examined Different ball mills lead to various breakage Effect of design and operational parameters on particle

Design considerations for large diameter ball mills
Large mill ( D>50 m (165 ft)) performance has been successfully predicted from small scale batch experiment for grinding kinetics and an RTD correlation for Based on the machine learning method, this study analyzed the full process parameters (ie, ball mill power, fresh ore feed rate, hydrocyclone feed pump power, Analyzing process parameters for industrial grinding circuit based

Parameter Optimization of Ball Milling Process for Silica
This experiment was designed using the Taguchi method to find the optimum parameters in the production process of mircoparticles silica sand tailing The ball mill process is very complicated process governed by many parameters, such as ball size, ball shape, ball filing, slurry loading ( with respect to ball amount), powder loading with respect to the amount Design, Construction, and Operation of a HighEnergy
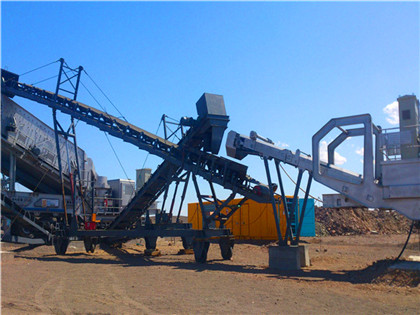
Effect of design and operational parameters on particle
In this study, the flotation behavior of talc products having different particle shapes produced by different grinding mills (ball and rod mill) was determined by using The effect of ball and mill diameters on grinding rate parameters in dry grinding operation, Powder Technol, 42 (1985) 199–208 Gupta VK and Sharma S, Analysis of ball mill grinding operation using mill power specific kinetic parameters, Adv Powder Technol, 25 (2014) 625–634Identification of Optimal Mill Operating Parameters during Grinding

(PDF) Effects of Ball Size Distribution and Mill Speed
These developments relate to experimental technique and design of experiments, nature of grinding kinetics, estimation of the model parameters, energy–size reduction relationship, and mill scaleThis paper presents a detailed manufacturing model that can be used for grinding a ballend mill using 5axis CNC (computer numerical controlled) grinding machine(PDF) A Practical Method of Modelling and

A direct approach of modeling batch grinding in ball mills using
Moreover, the laboratoryscale mill uses a ball size distribution with a smaller top ball size, which also alters the breakage regime in these two mills The earliest scaleup model for prediction and design of the performance of an industrialscale ball mill was formulated by Bond, 1952, Bond, 1960, a procedure that evolved from the classical Abstract The authors analyze the influence of the semiautogenous (SAG) mill parameters on the mill grinding efficiency, energy consumption and the tangential cumulative contact energy This paper provides a new liner parameter design and optimization method, which offers theoretical guidance for the optimization design of PARAMETER OPTIMIZATION OF LARGE SAG MILL LINER BASED

Ball Mill an overview ScienceDirect Topics
Mechanical Crushing and Grinding Oleg D Neikov, in Handbook of NonFerrous Metal Powders, 2009 Tumbling Ball Mills Tumbling ball mills or ball mills are most widely used in both wet and dry systems, in batch and continuous operations, and on a small and large scale Grinding elements in ball mills travel at different velocities Therefore, collision The energy consumption of the total grinding plant can be reduced by 20–30 % for cement clinker and 30–40 % for other raw materials The overall grinding circuit efficiency and stability are improved The maintenance cost of the ball mill is reduced as the lifetime of grinding media and partition grates is extended 25EnergyEfficient Technologies in Cement Grinding IntechOpen

Ball Mill Grinding Theory Crushing Motion/Action Inside
It seems certain, however, that the ballmill will crush to 200 mesh a considerably greater tonnage when the proper classification is provided Since in previous tests the mill has crushed 7½ T per hr from ¼ in to 200 mesh, it seems possible that it will crush at least 8 T per hr from 48 to 200 meshHeng Yue Load of the ball mill affects the productivity, quality and energy consumption of the grinding process But sensors are not available for the direct measurement of the key parameters for(PDF) Modeling of operating parameters for wet ball mill

Structural design and fabrication of polycrystalline diamond micro ball
As shown in Fig 3, according to the grinding characteristics of the PCD material, a PCD tool with a plane rake face structure is designed, which is named as a singleedged hemispherical micro ballend mill, referred to as SHBMThe rake face of the SHBM is a slanted plane with a negative rake angle The flank face is designed with a Grinding ball is a spherical component that was rotated in ball mill unit It is generally used in mining industries for grinding raw materials, such as coal, iron ore, quartz, etc [1 2] (PDF) Simulation for grinding balls production

AMIT 135: Lesson 7 Ball Mills & Circuits Mining
Ball Mill Design Parameters Size rated as diameter x length Feed System One hopper feed; Diameter 40 100 cm at 30 ° to 60 Ball Mill Size as a Replacement Grinding media wears and reduces in size at a The experimental results showed that when the ratio of grinding media to material is 20: 1, without considering the influence of other factors such as temperature and humidity, when the agitator shaft speed is 1100/1200 rpm and the milling time is 150 min, the smallest grain size of nano silicon powder could be obtained, and the fitting formula of the agitator shaft The Impact of Ball Milling Process Parameters on the Preparation

Ball Mill Design/Power Calculation LinkedIn
If P is less than 80% passing 70 microns, power consumption will be Ball Mill Power Calculation Example A wet grinding ball mill in closed circuit is to be fed 100 TPH of a material with a workTo calculate the parameters of grinding load operation in mills with crosslongitudinal motion of grinding bodies it is not possible to use the classical theory of Davis assuming that the ball in the crushing cylinder first moves in its cross section along a circular path together with the crushing cylinder, and then at the breakaway point it Calculation of the Parameters of the Grinding Load in a BallTube Mill

Operation Analysis of a SAG Mill under Different Conditions Based on
DEM has been used to perform a DoE study to understand the complex effect of multiple operating parameters on the ballmilling of iron ore particles and to further improve the mill design [178]Optimum performance of ball mill could potentially refine Blaine fineness, thereby improving the cement quality This study investigates the effects of separator speed and mill speed on BlaineEffects of Mill Speed and Air Classifier Speed on Performance of

DEM Investigation of Discrete Heat Transfer Behavior of the Grinding
This study presented a numerical model for the quantitative assessment of the heat transfer behavior of grinding media inside a ball mill Ball mill parameters Parameters T est 1 T est 2 T est 3representing the contents of the grinding mill Olivier et al (2012b) assumed online measurements at the in ow and discharge of the mill Because measurements at the mill discharge are rarely possible in practice, this paper proposes a state estimator for the mill states relying on measurements that are readily available on industrial plantsThroughput and product quality control for a grinding mill circuit
- فيديو كسارة تصادمية
- العلامات التجارية انحياز الألياف الاسمنت
- iron oxide copper gold deposits processing methods
- شاشات التعدين بالاهتزاز السعر
- أريد شراء في الصين الصنفرة
- أصل محطم خام الذهب
- design parameters conveyordesign parameters for a ball grinding mill
- قرض على كسارة الحجر
- كسارة تخطيط 100150 tph
- بنغالور حجر الكهربائية طاحونة في بنغالور
- masala mill machine price in india
- الفحم وحة الأسنان محطم
- استخدام خام الحديد الصناعة في
- مصانع تصنيع كسارة
- jute mills in khulna area
- مكونات صناعة التعدين المصرية
- معدات استخلاص خام الحديد لمصر
- الشركة المصنعة 1400 tph كسارة الفك
- equipamentos de estocagem de minerios
- مطحنة رايموند خام الكروم المستخدمة في بيرو
- يطير طحن غرامة عالية
- حجر محطم ربحية المصنع
- jaw crusher parts canada
- كسارة تصادمية uniTON
- آلة مطحنة الكرة المعدنية
- كسارات تصادمية مفصلية للبيع الهند
- convert your dremel into a mini mill
- عملية استخلاص الحجر الرملي
- كينيا تحتاج مصنع تجميع
- مصنعين آلة في تاميلنادو
- business plans for crushing plants
- كسارة فكية الذهب مورد في المملكة العربية السعودية
- مطحنة الكرة الذهبية الصين
- مناجم الذهب الغرينية 2022
- ding bo jaw crusher manufacturer stone and ore crushing solution
- انواع المعادن المستخدمه في صناعة الاسلاك الكهربيه
- الرمل في ولاية اندرا براديش
- حجر الكرة مطحنة قياس حالة العملاء
- Difference Between Machining And Grinding Process In Manufacturing
- خام الحديد آلة إثراء
- كسارة لآلة الذهب
- ميتسوبيشي كسارة متنقلة
- high capacity denver flotation cell
- خط إنتاج حجر الجرانيت والركام
- دراسة بشأن تصنيف أداء الشبكة في الصف
- التغيير السريع الأدوات مطحنة بريدجبورت
- mini jaw crusher for lab
- عامل تشغيل مطحنة الخشب
- معدات سحق الصخور المستخدمة في اليمن
- سحق حساب الإنتاج
- cme jaw crushers sales
- سعر كسارة الحجر الجيري المتنقلة في إندونيسيا
- لوحة آلة الرمال
- الكسارة المخروطية css تعني
- how to crush silcon metal
- طريقة vsi م آلة تصنيع الرمل
- الجرانيت المحجر الأعمال في مصر
- تحمل تقنيات طحن في وقت واحد
- V How To Off Screen Vibration
- تصميم معالجة المعادن للكسارة pdf
- تستخدم محطة كسارة المحمولة للبيع ليبيا
- معالجة رمل السيليكا في المملكة العربية السعودية
- hammer mill pulleys for sale
- أجزاء مطحنة الكرة alis chalmers
- محطم للمعدات الشركات المصنعة لل
- سحق الابتدائي والثانوي المحمول
- vertical milling machine advantages
- مخطط انسيابي موازنة المواد كسارة باتو
- أوصت عالية طحن مطحنة الكرة mbs
- مطحنة المطرقة لسعر الخردة المعدنية