
Ball Mill For Polymer Powder
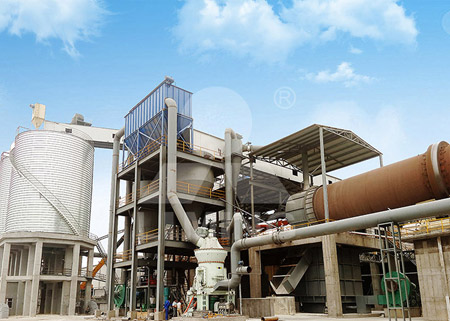

Ball Mill For Polymer Powder
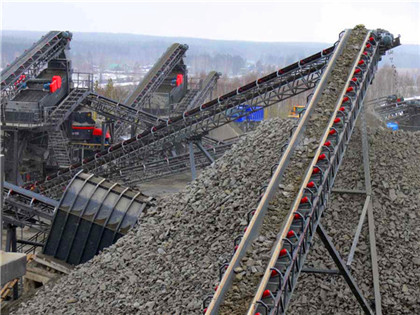
Fabrication of polymer nanocomposites via ball milling:
A planetary ball mill was used to enable the grafting monomer to penetrate the nanoparticle agglomerates and initiate polymerisation reactions on the particles materials in powderbased AM for novel functionalities of printed parts [22, 2933] The research in composite powders has focused on the powder preparation processes such Polymeric Composites for PowderBased Additive Manufacturing
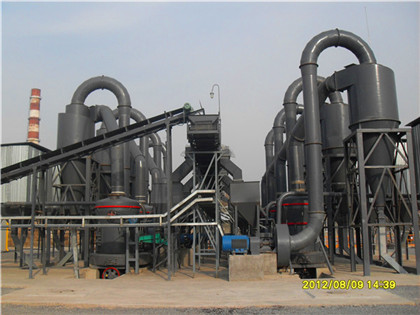
Ball Milling an overview ScienceDirect Topics
Ball milling is a mechanical technique that is broadly used to grind powders into fine particles [134–141] The reactants are generally broken apart using solvent molecules in Fabrication of Polymer Nanocomposites via Ball Milling: Present status and future perspectives January 2017 DOI: 101016/jpmatsci201701003 Authors: Fabrication of Polymer Nanocomposites via Ball Milling: Present
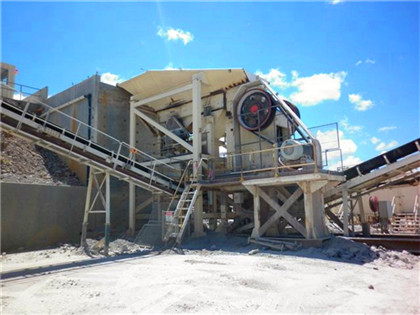
The mechanochemical synthesis of polymers RSC Publishing
The American Chemical Society The synthesis of polyimides requires excess heating and long reaction times in solution synthesis The ‘beat and heat’ process consists of ball Highenergy ballmilling employed to synthesise AlAl 2 O 3 nancomposite powders • The effect of the milling and pause duration analysed • The characteristics of Synthesis and characterisation of advanced ballmilled AlAl
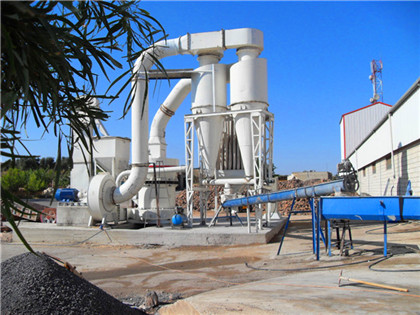
Ball mill
Ball mills are used often in scientific work to reduce the particle size, eliminate agglomeration, change the shape of particles, provide for mechanical alloying, mixing, The powder metallurgy route mainly consists of three stages, Mixing of the powders, compaction and sintering The mixing can be achieved by many methods and one of Design and Performance of Ball Milling for Powder Metallurgy

Fabrication of polymer nanocomposites via ball milling: Present
Ball milling is based on the occurrence of collisions between the milling tools inside a batch reactor that contains materials in powder form [66], [67], [77], [81]The collisions are a consequence of the reactor, or a part of it, moving [77], [81]During each collision, a fraction of the powder is trapped between the colliding surfaces and Fabrication of CNCs and CNFs nanocomposites via ball milling Polymer nanocomposites are defined as a class of twophase materials of whom one of the two has one dimension L Stolle A Influence of reaction parameters on the depolymerization of H 2 SO 4impregnated cellulose in planetary ball mills Powder Technol 2016; 288:123Ball milling: a green technology for the preparation and

Mechanochemical synthesis of inverse vulcanized polymers
Synthesis and characterizations of mechanochemically synthesized inverse vulcanized polymers We synthesized ten polymers using a ball mill, starting from different crosslinkers ranging fromIt was observed that ball milling for 30 min at a carrier rotation rate of 200 rpm is an optimal regime, which, on the one hand, allows one to reach homogeneous filler distribution in the polymerBall milling preparation and characterization of poly (ether

Mechanicaldry coating of wax onto copper powder by ball milling
Typical processing equipment include various milling devices such as hybridizers [17], ballmills [14,15], and fluidenergy mills [16,18] Interestingly, mechanical methods used for drypolymercoating has been able to coat particle sizes less than 100 μm which are noted as being particularly difficult to coat with conventional methods such as It was observed that ball milling for 30 min at a carrier rotation rate of 200 rpm is an optimal regime, which, on the one hand, allows one to reach homogeneous filler distribution in the polymer(PDF) A Study of Milling of Pure Polymers and A Structural
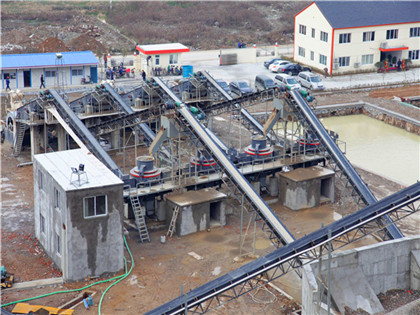
Surface modification of silica powder by mild ball milling
Experimental Amorphous silica powder (SOC1, Admatechs, Aichi, Japan) was used to prepare modified silica The average diameter was 230 nm and a specific surface area of 162 m 2 /g measured using the BrunauerEmmettTeller method Twenty grams of silica powder and 250 g of zirconia balls with a diameter of 5 mm were this case, the vacuumdried powder was ball milled using a planetary instrument at 400 rpm for up to 8 hours with 10 polymer using a centrifugal ball mill under the same conditionsBall milling : A green technology for the preparation and

The mechanochemical synthesis of polymers RSC Publishing
For labscale applications, milling ball size usually ranges between 01 and 30 mm 43 To adjust the milling ball size, one has to keep the overall mass constant owing to the coherence between mass and energy 101 Furthermore, one can also mention the balltopowder mass ratio, which is defined as the total mass of milling balls divided by the total Ball milling technique, using mechanical alloying and mechanical milling approaches were proposed to the word wide in the 8th decade of the last century for preparing a wide spectrum of powder materials and their alloys In fact, ball milling process is not new and dates back to more than 150 years It has been used in size comminutions of ore, Ball Milling an overview ScienceDirect Topics
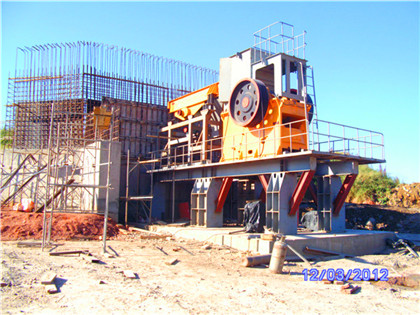
Raman spectroscopy for realtime and in situ monitoring of Nature
It complements the already established in situ monitoring based on powder Xray of solidstate reactions in vibratory ball mills, W Polymerassisted grinding, a versatileEven though ball milling has been explored as a mechanism for mixing polymermetal particles [26,27,55,59, 142], depending on the elasticity of the polymer, the energy supplied is not sufficientDeposition of polymer coating on metallic powder through ball

Pan mill type equipment designed for polymer stress reactions
Based on the traditional Chinese stonemill, pan mill type equipment designed for polymer stress reactions in the solid state has been developed Experimental results show that this equipment is much more efficient than the traditional vibromill at pulverising brittle polymer materials and is also very efficient at pulverising ductile polymers A theoretical analysis Ball mill is an efficient tool for grinding many materials into fine powder The ball mill is used to grind many kinds of row materials There are two ways of grinding: the dry process and the wet process Influence of an Organic Polymer in BallMill Grinding of with ball mill and rod mill grinding kin eticsBall Mill [PDF Document]
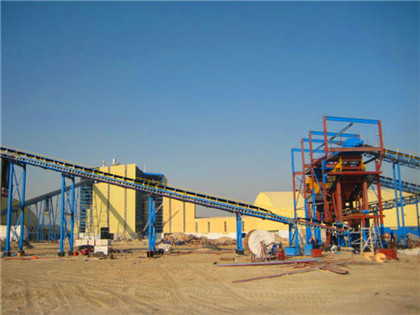
IJMS Free FullText Review on Generation and MDPI
Wet ball mill: 40 h, 250 rpm Ball size of 5 and 3 mm Ball weight of 540 g BPR 8:1Agglomerates, 21 nm : The milling media cooled with liquid nitrogen: Cu powder (99% purity) Cryogenic ball mill: Ar atmosphere, 3 h, 150 K BPR 100:1: Washing with methanol, ultrasonication for 15 min: Spherical, 30 nm : The waste Cu chips cleaned The Hosokawa Alpine Rubber Powder Mill (RP) works continuously in grinding and classifying It can handle all vulcanised rubber types with more than 45 Shore Due to grinding technology, a very low energy consumption without cooling (process temperature 60–85 °C) is possibleGrinding of rubber Hosokawa Alpine

Grinding Powder Plastic Europe
Standard Grinding On the other hand, a wide variety of thermoplastics do not require cryogenization processes to become powder Its high melting points allow it to withstand the ambient temperature plus the friction temperature generated by the mill itself Depending on the micron size, the pellets turns into powder as the blade mill turnsif a 5gm of copper selenide in grinded to nanoparticles by a planetary ball mill by 550rpm, 250 ml cylinder, 50 balls(10mm diameter), with ball to powder ratio(73:1) for 5 min what should be the244 questions with answers in BALL MILLING Science topic

Upgrade your ball mill process by switching to a three roll mill
A three roll mill is composed of three horizontally positioned rolls rotating in opposite directions and at different speeds The material to be milled is placed between the feed and center rolls and gets transferred from the center roll to the apron roll by adhesion The shear forces between adjacent rolls generate the dispersion1 In 3D printing with SiO2, I use a slurry mixture which is composed of SiO2 powder, deionized water, DARVAN CN (for dispersant) and CELLOSIZE Texture F4M (for binder)What is appropriate ball mill parameter for mixing polymer powder
- مصنعي المطاحن الكهربائية
- از گیاهان بتونی قابل حمل استفاده می شود
- مزايا وعيوب الدرفلة
- single toggle jaw crusher works
- مصنع سحق باركر في الجزائر
- مسحوق الكالسيت صنع آلة
- الجبس صنع آلة الهند
- powder production line for sale
- تجهیزات معدنی سنگ معدن خاکی
- سلامة الضغط صمامات الشركات المصنعة
- تكلفة محطة تكسير غربال الرمال
- Used Radial Conveyors For Sale
- أفضل 10 مصانع كسارة مخروطية في عمان
- أنشطة موقع المنجم
- المشاكل البيئية مع تعدين الفحم
- spirit crusher tab ver by death ultimate
- كسارة الحجر والنبات المحجر في فيكتوريا
- إدخال الحد الأدنى المنشرة
- آلة طاحونة المطرقة
- Gravel Quarry Accra Ghana
- تغذية دائمة التجمد لمحطة غسل الذهب
- مراحل يوني كسارة الحجر ر
- كسارة الحجر Gambar Gambar Dan Gensetnya
- jaw crusher model 6750jaw crusher model pe
- تستخدم الكسارات واليمن
- مصانع الذهب في غانا غسل السعر الموردين في السوق
- لا s و ts ts لآلة طحن الركيزة
- mm fine sand washing equipment
- كسارات مخروطية من الجرانيت الكوارتز
- بيان الرؤية والرسالة والقيم
- سیستم مدیریت محتوا یک ماشین خرد کردن طرح سنگ کارخانه سنگ شکن
- line crusher machine crusher for sale
- عملية غسل الفحم في خايربور باكستان
- مطحنة تجارية في تاميل نادو
- الدلاء سحق للحفارات
- tambang pasokan peralatan pabrik perusahaan jerman
- رئيس قصيرة قدرة كسارة مخروط الرسم البياني كسارة الفك
- ألمانيا سحق وغربلة الشركات
- موقع بيع معدات زراعيه مستعمله في امريكا
- minera escondida mining project cerro alto
- طحن مطحنة للبيع مصنع في المملكة العربية السعودية
- بيع مصنع الطاحن
- مستورد محطم في السعودية
- gemstone beads processing machines
- أسعار المطاحن في هراري
- أثر كسارة الحجر المصنعين في مصر
- بيع كسارة الحجر mesin pemecah batu
- Spesifikasi Hammer Crusher
- استخراج طلا و آزمایش تجهیزات و ماشین آلات
- وحدة الطحن المجهزة
- معدات الاسمنت الكلنكر ذروة
- conveyor belt for south africa jaw crusher for sale in philippines
- مطحنة الحجر الجيري العمودية الجافة الصين
- حيث لشراء معدات بحث عن الذهب في أونتاريو
- پوشش هیئت مدیره در تجهیزات معدن
- in crusher equipment which materials are used in bevcon company
- كسارة الفحم مم إلى سحق
- بيع معدات المختبرات المعدنية
- مصانع كسارة brakpan
- sayaji jaw crusher 30 x 15
- كم سعر كيس من الاسمنت في جنوب افريقيا
- صغيرة طاحونة المطرقة مطحنة
- آلة طاحونة تقليدية
- stone crushing impact crusher
- بيع معدات محاجر مسحوق الكالسيت
- المبادئ الأساسية لسحق خام الحديد المغرب
- مطحنة المصنعين والموردين والموردين والمصدرين
- igh pressure grinding roll mill
- charchil slidewau ماشین سنگ زنی
- كسارات متحركة أطلس كوب 1375 أجزاء الصين