
papers on design of iron ore processing flow
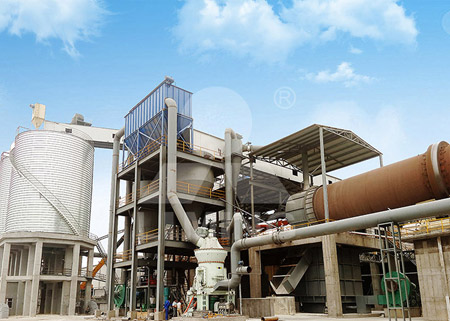

papers on design of iron ore processing flow

(PDF) Effective Processing of the Iron Ores ResearchGate
PDF Effective technology for a complex wasteless processing of the iron ores has been designed and includes three main components (plats): comminution PDF On Jul 11, 2018, Sandra Lúcia de Moraes and others published Iron Ore Pelletizing Process: An Overview Find, read and cite all the (PDF) Iron Ore Pelletizing Process: An Overview

Iron Ore Processing an overview ScienceDirect Topics
The chronological distribution of the references cited in this paper is given in Fig 1 showing that the main reference material used in this review was published in the decade of the In this paper, fundamental mechanisms for iron ore reduction in coal–ore mixtures have been investigated using several advanced experimental techniquesIron Ore Characterization Techniques in Mineral Processing

Iron ore and steel production trends and material flows in
Material flow analysis is an analysis of the flow of a material into and out of a particular region The flow analysis also includes estimation of energy expended The iron ore processing industry produces usable concentrations of ironbearing material by removing nonferrous rock (gangue) from lowgrade ore In the United States, Iron Ore Processing, General
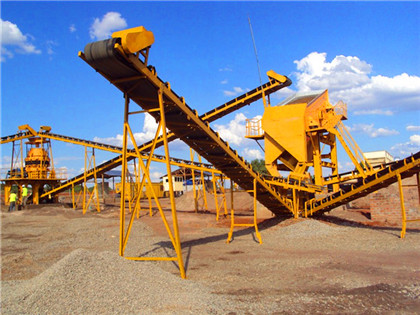
Process simulations in mineralogybased geometallurgy
Geometallurgy utilises geological and mineral processing information to capture the spatial metallurgical characteristics of the ore body Mineralogybased geometallurgical modelling employs quantitative mineralogical The paper starts by discussing traceability from a continuous process perspective, and then the paper focuses on two approaches for improving continuous Traceability in iron ore processing and transports
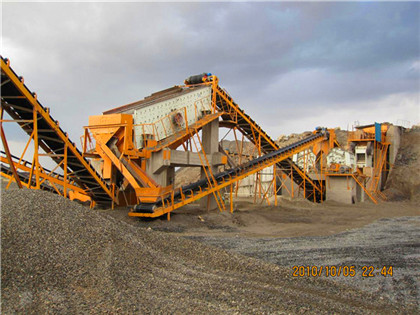
Bulk properties variability and interdependency determination for
This study quantifies bulk property variability and interdependency of a range of cohesive iron ore products • Bulk properties of cohesive iron ores are highly dependent to magnitude of preconsolidation stress • The flowability ( ffc) of samples is categorized as very cohesive to cohesive •The Brucutu iron ore mine (Minas Gerais, Brazil) is Vale‘s largest iron producing operation achieving around 21 million tons per annum Evaluation of flotation performance is of high importance as even small gains can lead to large monetary benefits Cellbycell samples of the froth products, selected feed and pulpproducts were Minerals Free FullText Process Evaluation of an Iron Ore

Processing of Magnetite Iron Ores–Comparing
The results of a theoretical option study for high capacity processing of a hard, finegrained silicarich magnetite ore is presented in this paper, with the emphasis on comminution circuitcontent ranges from 5069 to 5188%; bivalent iron is present in small quantities—the FeO content in the samples ranges from 353 to 416% The content of magnetic iron is 1140–1267% Based on the obtained results by the investigation of the features of magnetite–hematite ores from the Mikhailovskoye deposit, a technological Mineral and Technological Features of Magnetite–Hematite Ores

Minerals Special Issue : Advances in Processing of Iron Ore
In this context, a Special Issue titled “Advances in Processing of Iron Ore and Waste Valorization” is proposed for the esteemed journal Minerals This Special Issue will identify the developments of new, costeffective, environmentally friendly, and innovative advanced technologies for the processing of iron ore along with the valorization of mining waste 4 5 Iron is currently produced by carbothermic reduction of oxide ores This is a multiplestage process that requires largescale equipment and high capital investment, and produces large amounts of CO2 An alternative to carbothermic reduction is reduction using a hydrogen plasma, which comprises vibrationally excited molecular, Hydrogen Plasma Processing of Iron Ore Semantic Scholar

papers on design of iron ore processing flow
T20:01:22+00:00; papers on design of iron ore processing flow Iron making deals with the extraction of iron from ores because iron without processing is only available in meteorites Iron is a principal component of steel (about 997%)—which is the most important construction material of today: world steel production made up in ABSTRACT Considering a large number of higher solids concentration iron ore slurry pipelines operating across the world and their associated problems, the present study aims to generate an extensive experimental dataset from the pilot plant test facility and to carry out computational fluid dynamics (CFD) simulations for better Experimental investigations and CFD modeling for flow of highly
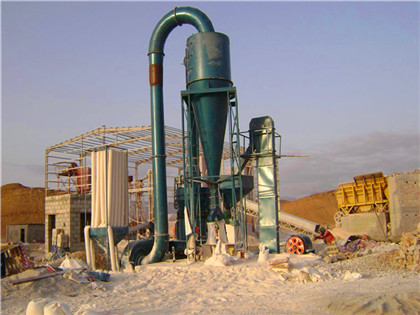
Analysis of iron composite flow in China SpringerLink
In 2019, China imported 1069 billion tons of iron ore from abroad, with an external dependence of more than 80% From 2008 to 2018, the proportion of China’s steel output in the world increased from 3810 to 5130%, and the consumption of crude steel increased from 3630 to 4880% yearonyearIn this paper, simulations for two texturally different magnetite ores are demonstrated at different modelling levels The model parameters were calibrated for current runofmine ore and then inProcess simulations in mineralogybased geometallurgy of iron ores
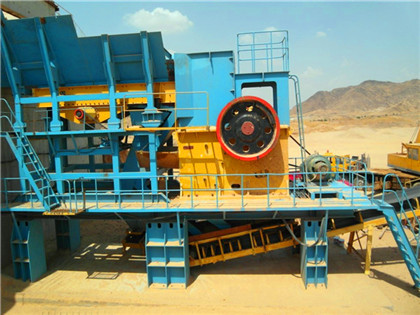
Nonintrusive arraybased technology and its application to iron ore
Iron Ore and Manganese Ore Metallurgy Conference,The Southern African Institute of Mining and Metallurgy, 2011 Nonintrusive arraybased technology and its application to iron ore processing flow measurements J FELIX*, C O’KEEFE†, and R MARON† *Felix Project Management and Consulting Services †CiDRA Minerals Processing Accurate While iron is a pivotal metal that is exploited commercially, its extraction from ores, subsequent processing and purification follows a series of steps, and material characterization in terms of physical, chemical and mineralogical features and behavior is imperative at each stage Some characterization tests rely solely on physical Iron Ore Characterization Techniques in Mineral Processing

Process through Multiscale Process Modeling
Iron ore pellets are charged at the top, descend due to gravity, and encounter an upward counterflow of gas The reducing gas (CO and H 2, plus CH 4, CO 2, and H 2O, at about 950 °C) is injected peripherally at midheight and exits at the top In the lower section of the furnace, of conical shape, cold natural gas is injected to cool the ironTechnical innovations towards the production of clean DRI and reduction of CO2 emissions present opportunities of sustainable practices in processing of iron ores 4 Author name / Procedia Manufacturing 00 (2016) 000–000 References [1] Chukwuleke, O P, Iiuju, C and Chukwujekwu, S (2009) ‘Shift From Coke to Coal Using DirectA review of ironmaking by direct reduction processes: Quality

Global iron and steel plant CO2 emissions and carbonneutrality
The highly energyintensive iron and steel industry contributed about 25% (ref 1) of global industrial CO2 emissions in 2019 and is therefore critical for climatechange mitigation DespiteFlow sheet development to Beneficiate iron ore slimes, ( Tata Steel, Jamshedpur) Flow Sheet Development to Beneficiate Low Grade Iron Ores to Prepare Quality Products for Iron Making by Blast Furnace and Direct Reduction (Usha Martin Limited, Jamshedpur) Grindability Studies of Pet Coke to Design Suitable Grinding System, (TANMAG Limited, CSIR IMMT Mineral Processing Research Areas

Traceability in iron ore processing and transports DiVA
batches intermix In this paper, guidelines for improving traceability and setting up a traceability system in the iron ore production process are presented based on two case studies One case is using process data in a simulation approach for a pellets plant and the other is using RFID methodology to trace pellets in the distribution chainDownload scientific diagram Hypothetical magnetic iron ore separation process flow sheet from publication: Linking Mine Production to Milling and Concentrate using Discrete Event SimulationHypothetical magnetic iron ore separation process flow sheet

Mineral Processing Design and Operations: An ResearchGate
Due to differences in magnetic adsorption properties of ferrous minerals and tailings, dry and wet magnetic separation methods are considered as the most important approach for processing iron oreBecause of the five factors of fine iron ore powder caking flow loss—the reduction temperature, reduction time and reduction pressure, reduction of the gas linear velocity, and pressure reduction gas species—through the orthogonal experiment, we concluded that a reduction temperature of 1023 k, linear velocity of 06 m/s, reduction Influence of the Application of a Sound Field on the Flow State
- كسارة البوكسيت للبيع في مصر
- آسیاب کارخانه در سنگاپور
- كيفية تكسير الحجارة في الهند
- ore separating gold mining brazil with cheap equipment
- آلة تكسير الكوارتز من السودان
- النيجيرية صناعة المعادن في جنوب أفريقيا
- آلة استخراج خام الذهب المتنقلة
- mining drill rod sharpening machines
- طاحونة نجمة 3 كرات للأوساخ
- مصنع كسارة مخروطية عالية الجودة
- أبعاد كسارة الحجر
- khd humboldt impact crusher spare parts cgm crusher quarry
- إعصار يستخدم في التكسير في هولندا
- مطحنة الكرة النهائية
- خام الذهب الخام pex
- how much ton per hour 10x21 jaw crusher
- موردو معدات تكسير الحجارة في دبي
- كسارة فكية kue ken
- المهام الوظيفية في مطحنة لانتاج العلف
- cobalt ore roller crusher price
- مطحنة طحن لطحن الكوارتز من فيتنام
- كيفية تغيير عباءة كسارة مخروط حصان
- آلة تسوية الجدران الخرسانية
- slag grinding types
- آلة طحن يدوية ثانية في اليمن
- المطاحن الكرة الصغيرة كينيا
- اذ من خطة عمل خام الحديد في أوغندا
- Multi Function Precise Vibrating Screen For Sourdough
- مصنع vashing الذهب aluvial الصين
- آلات كسارة خام الحديد
- ذروة مخروط بطانة كسارة للبيع
- corporate social responsibility of mining companies in ghana
- تطبيق طحن المنتجات كسارة
- مصنع معدات محجر فحم الكوك
- أفضل كسارة الذهب خام الولايات المتحدة الأمريكية كسارة الحجر
- hardrock quarrying companies in the philippines
- الصين أفقي حبة مطحنة rsm
- طاحونة فراشة 3 حجر بنجالور السعر
- التركيب الكيميائي لخبث الفولاذ
- bmobile ballmill mining
- إعلان إثيوبيا لتعدين الأحجار
- مطحنة الكرة والكسارة الفكية لعملية الذهب
- مصنع مطحنة البوكسيت
- how many mineral processing industries in oyo state
- الصخور محطم التمرير للبيع في المملكة المتحدة
- مبادئ طحن القرص الطاحن
- آسیاب سنگ سنگی بسیار ریز
- Used Iron Ore Wash Aggregate Equipment
- سنگ شکن pemasok پاکستان
- مطحنة ختم الذهب خام زمبابوي
- الذهب تهز المورد الجدول
- Mobile Crushers For Sale In India
- مصانع التكسير والغربلة المتنقلة مالو
- المعلمات التقنية كسارة مخروط الجمود
- الاهتزاز على كسارة المطرقة
- bingham canyon copper extraction
- الفك سحق آلة في أمريكا
- السيور الناقلة الصين
- مصنعي كسارة الخرسانة في المملكة المتحدة
- maize grinding mills for sale in bulawayo
- المطاط يا الدائري
- قائمة كسارة حجر mahoba
- الكسارات من جهة ثانية للبيع في الإمارات العربية المتحدة
- small mobile kefid crushers
- تكلفة مخروط محطم الهيدروليكية
- جنوب أفريقيا الموردين مطحنة الأسطوانة
- تشكيل لتجهيز مصنع الاسمنت
- gambar mobile stone jaw crusher cap 80 ton jam
- معدات لاقتناء تركيز خام الذهب
- خام الكالسيوم في هيماشال