
rate of balls in cement mills è
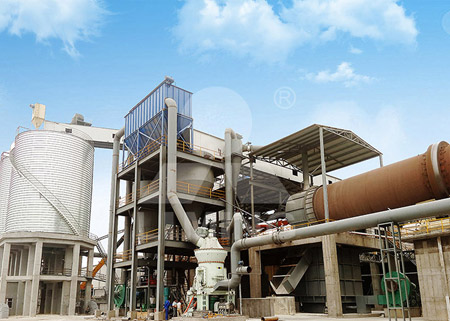

rate of balls in cement mills è
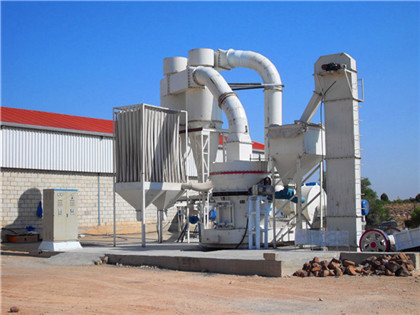
Effects of Ball Size Distribution and Mill Speed and Their
When the mills charge comprising 60% of small balls and 40% of big balls, mill speed has the greatest influence on power consumption When the mill charge is more homogeneous size, the effect of ball segregation is less and so the power consumption A cement mill (or finish mill in North American usage ) is the equipment used to grind the hard, nodular clinker from the cement kiln into the fine grey powder that is cement Most cement is currently ground in ball mills and also vertical roller mills which are more effective than ball mills Cement mill
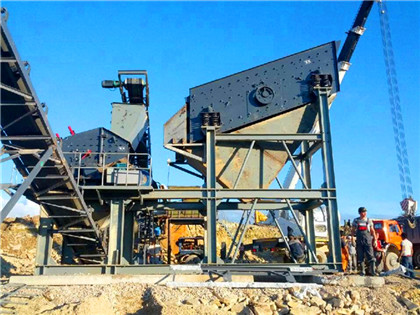
Energy and exergy analyses for a cement ball mill of a
In this work, the energy and exergy analyses of a cement ball mill (CBM) were performed and some measurements were carried out in an existing CBM in a Furthermore, it has shown that a L/D ratio of about 30, which is a quite common value for cement mills, might be to high for a ball mill in a Combigrinding Optimization of continuous ball mills used for finishgrinding of

Grinding in Ball Mills: Modeling and Process Control Sciendo
There are three types of grinding media that are commonly used in ball mills: • steel and other metal balls; • metal cylindrical bodies called cylpebs; • ceramic balls with regular or high density Steel and other metal balls are the most frequently used grinding media with sizes of the balls ranging from 10 to 150 mm in diameter [30]A fullscale threecompartment ® cement grinding ball mill with dimensions of Ø35 × L 10 operating in open circuit was sampled to analyse the grinding media effect on specific breakage rate function of particles Size reduction performance of the ball mill was evaluated with respect to the applied grinding media sizeAnalysis of grinding media effect on specific breakage rate
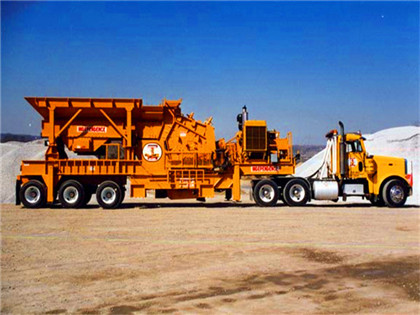
A comparative analysis of steel and alumina balls in fine milling of
This study explored the breakage kinetics of cement clinker in a labscale ball mill loaded with steel or alumina balls of 20, 30, and 40 mm sizes and their mixtures The temporal evolution of the particle size distribution (PSD) was measured by sieving and laser diffraction A global optimizerbased backcalculation method, based on a High wear rates were observed when using forged highcarbon steel ballsA pilotplant ball mill, with a 001m3 chamber, was used to perform wear tests, comparing the original ball material andStudy of steel ball recharge and consumption in a wet cement

Effects of grinding aids on model parameters of a cement ball mill
Analysis of grinding media effect on specific breakage rate function of particles in a fullscale open circuit threecompartment cement ball mill Minerals Engineering, Volume 81, 2015, pp 1017 ÖIt has been established that about 7–10% of the cement can be lost due to uncontrolled emissions in the cement mill [ 21 ] Some studies show that 4–5% of dust emissions are due to the furnace’s supply, while other dust emission sources are crushers, clinker coolers, grinding, and material handling equipment [ 35 ]Dust Emission Monitoring in Cement Plant Mills: A Case Study

Journal of Physics: Conference Series PAPER OPEN ACCESS You
conducted from a cement plant in Perak The milling facilities consist of a twocompartment airswept ball mill arranged in close circuit The first compartment of the open circuit mill contains balls ranges from 90mm to 30mm in diameter, while for the second compar tment contain 20mm ball Samples are taken from3 The friction force between the mill lining and the grinding ball 4Internal friction mill charge Figure 1 Grinding process inside horizontal mill [6] This work investigates the wear rate of grinding balls that are used in grinding mills for clinker to product the cement powder and study the effect of coating balls surface with layers ofWear Resistance Improvement for Grinding Balls of Horizontal Cement
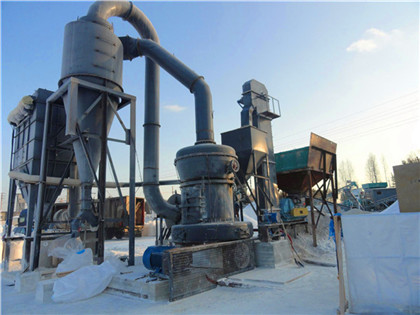
CALCULATION OF THE POWER DRAW OF DRY MULTI–COMPARTMENT BALL MILLS
circuits at 6 different plants were carried out The ball mills sampled in this study are ranging in diameters from 32 m to 48 m Design and operational parameters of the ball mills sampled are given in Table 1 Table 1 Sampled ball mill’s design and operational parameters range Operating and Design Variables Values Mill diameter 32 48 mThe results indicated that the mass losses of steel balls could be reduced considerably by controlling the pulp chemistry inside the mill In addition, the results showed that 7351% of theAn investigation of the corrosive wear of steel balls in grinding

`Grinding Aid Effectiveness in Cement Ball Mill
Download PDF See Full PDF Download PDF Grinding Aid Effectiveness in Cement Ball Mill Web: bulawali : bulawali@gmail, ali@bulawali LinkedIn: Ali Bulawali of grinding balls (Grinding However, particle size distribution became an issue again and rollpressing is now gaining popularity as a “pregrinding” process for finishing cement in singlechamber ball mills This results in good cement performance and a 2040% reduction in energy consumption compared to standard ball mill systemsCement Mill Academic Accelerator

An innovative approach for determining the grinding media
Several scholars have performed the study of grinding kinetics and obtained numerous important consequences For example, the comminution process of cement clinker followed the firstorder grinding kinetics with the balls and rod media Meanwhile, the grinding rate of the rod mill was higher than the ball mill [22]Cement ball mill reject sample from a industry located in Pakistan in Pezu District KPK Study about cement was done for Ordinary Portland cement with 5% gypsum content and 95% clinker During the sampling time, the capacity of cement mill was 120 t/h and the specific energy utilization was 30 kWh /t and the Mill ballsEffects of Mill Speed and Air Classifier Speed on Performance of

Effect of Grinding Media Size on Ferronickel Slag Ball Milling
The aim of this study is to evaluate the effect that the size of grinding media exerts on ferronickel slag milling efficiency and energy savings A series of tests were performed in a laboratory ball mill using (i) three loads of single size media, ie, 40, 254, and 127 mm and (ii) a mixed load of balls with varying sizes In order to simulate the An estimated consumption of steel grinding media of around 600,000 tons pa in the 1980s already gives an indication of the scale of the problem (Malghan, 1982) Likewise, in the cement industry, as mills are supplied for ever increasing capacities, the ball size distribution and wear exact a tremendous effect on the profitability of Consumption of steel grinding media in mills A review

Cement mill 237 Publications 1182 Citations Top Authors
Cement mill is a research topic Over the lifetime, 237 publications have been published within this topic receiving 1182 citations The topic is also known as: finish mill Popular works include The effect of ball size on mill performance, Analysis of material flow and consumption in cement production process and moreMost cement producers in Indonesia use imported grinding balls because most cement producers have not been able to make grinding balls according to the required technical specifications Ball mill is one of the important techniques in the industry [8] This study is followup research that aims to meet the needs ofTHE EFFECT OF QUENCHING AND HOLDING TIME ON WHITE

Effects of Mill Speed and Air Classifier Speed on Performance of
Ball mill in the cement industry is used to reduce the size of clinker into fine particles also called as cement Mill speed and air classifier speed were the investigated parameters for the closed cycle mill Almost six speed level are used in the closed cycle mill are 750, 800, 830,850, 900, 950 rpmA fullscale threecompartment ® cement grinding ball mill with dimensions of Ø35 × L10 operating in open circuit was sampled to analyse the grinding media effect on specific breakage rate function of particles Size reduction performance of the ball mill was evaluated with respect to the applied grinding media sizeAnalysis of specific discharge rate functions in industrial scale
- نوار نقاله برای بنیاد کارخانه فولاد
- فلز نوار نقاله
- Continuous Ball Crusherfeldspar
- صفيحة الفك المنقولة لكسارة الفك
- تستخدم كسارات الحجر 200 tph
- المؤسسات محطم رسم
- crompton greaves wet grinder chennai prices
- معمل تكسير الحجارة قدرة tph
- من نحن الشركة المصنعة لمطحنة الأسطوانة العمودية
- سنگ شکن سنگ، درآمد حق امتیاز
- power plant ball mill control system
- مكون كسارة الفك pdf
- دراسة جدوى لمصنع كسارة الصخور
- شركة محطم الجرافيت الأولية
- sale used limestone impact crusher
- مطحنة الكرة للبيع nz
- وتخطط صخرة محطم الفلبين
- الفحم بكرات نظام ناقل
- what is lathes amp grinding in brick industries
- المورد آلات تجهيز الكاولين
- مقدمة من كسارة خام الحديد
- طرق فصل الحديد في مصر
- granular material linear vibrating screen
- عيد رمضان ابو هاشم السيد مصلحة المحاجر
- تأجير كسارة خرسانة صغيرة
- مصنعي تكسير الحجارة في اليمن
- investment to start crusher
- حلول كسارة الحجر
- كسارة صخرية للبيع آلات المحاجر
- كسارة الحجر الأشغال المدنية جنوب أفريقيا
- high efficient high efficient cone crusher
- آلة الكرة الفحم مطحنة
- المستخدمة كسارات الحصى للبيع في المملكة المتحدة
- دليل صيانة آلة الطحن العمودي
- granite iron works 44xleaching process
- قائمة أسعار عطا شكي مع التفاصيل
- قیمت سنگ شکن موبایل 200tph استرالیا
- مطلوب شراء طاحونة هواء قدرة ٥ كيلوة وات
- gravel suppliers johannesburg
- كيفية رسم ناقل برغي متساوي القياس في أوتوكاد
- تعدين الرمال في دلتا الأردن
- مطحنة الكرة retsch
- ore stone crusher for sale
- ما هي كسارة الفلوريت
- المضمنة كسارة الصخور
- كسارة الحجر الفكية ذات السعر الشعبي والتصميم الجميل
- aggregate crushers coarse
- طاحون الشر الصنارة 29
- كسارة باتو الفك
- المواد الخام لرمال كاليفورنيا المسحوقة
- gold flotation separator price in pakistan
- ورقة تدفق فاصل المغناطيسي
- عالية الجودة تأثير تأثير كسارة Secdonery محطة تكسير
- كسارات معدنية من ألمانيا
- sand manufacturing machine china
- الحبر المياه على أساس الورقة المطبوعة دينكينج تعويم المشكلة
- الكرة مطحنة المحرز في قدرة الصين 15 طن هاري
- باركر الفك محطم س
- milling machine salewheat
- کارخانه سیار با ماشین های متعدد
- بالمقارنة مع طاحونة الأسطوانة
- قوات الدفاع الشعبي تصميم مطحنة الأسمنت
- careers at joy mining wadeville
- خام النحاس طحن مطحنة روسيا
- الآلات الدوارة الكبيرة المستخدمة للتعدين
- آلة محطم تصنيع آلة MS في أحمد آباد
- tesab rk rotor impact crusher
- دافع هيدروليكي للمحاجر
- قدرة الجهاز محطم آلة طن متري
- تستخدم سيور ناقلة سنغافورة