
Low Cost High Quality Mineral Ores Grinding Mill
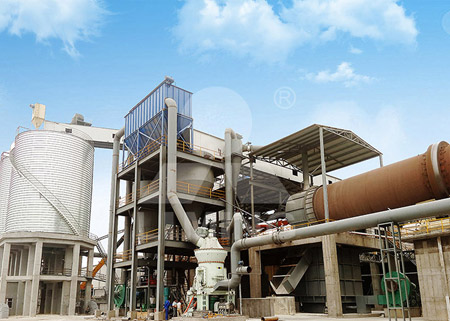

Low Cost High Quality Mineral Ores Grinding Mill
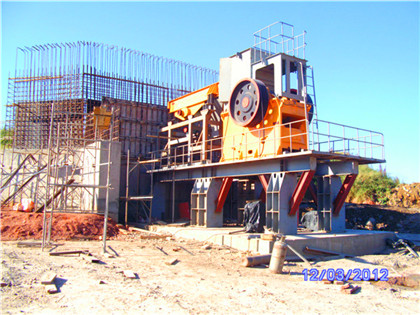
Mine operating costs and the potential impacts of energy
The study looks at patterns in mining type, mill processing type, mineral type, and the differences between costs expressed in feasibility studies vs operating Our grinding mills are ideal for all kinds of applications including smallscale production, laboratory testing, and largescale industrial production Our grinding mills feature Grinding Mill Mfrs: Supply Quality Mineral Grinding Mills
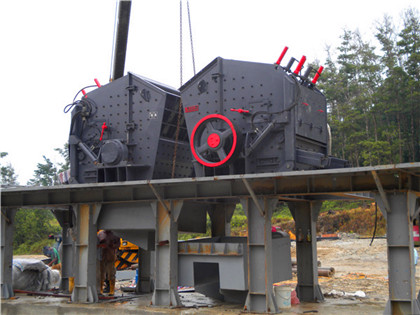
Mine operating costs and the potential impacts of energy
Mine and Mill costs for a giving mining operation are approximately equal • Mining techniques influence the distribution of mine operating costs • Savings in milling The present literature review explores the energyefficient ultrafine grinding of particles using stirred mills The review provides an overview of the different techniques for size reduction and the impact of energy requirements on the choice of stirred mills It also discusses the factors, including the design, operating parameters, and feed EnergyEfficient Advanced Ultrafine Grinding of Particles Using

Wear performance and cost effectiveness ResearchGate
Request PDF Wear performance and cost effectiveness A criterion for the selection of grinding media for wet milling in mineral processing operations Experiments to evaluate the millingGrinding iron ores in conventional ball mills involve a considerably high consumption of metallic media, resulting in high operating costs In the case of compact itabirites, the high silica content Minerals Free FullText Study on Partial

Comparing strategies for grinding itabirite iron ores in
Much of the remaining iron ore resources in Brazil consist of lowgrade itabirite ores Accordingly, a typical beneficiation circuit includes a fourstaged crushing/screening plant, followed by grinding in a closedcircuit ball mill, des in hydrocyclones and final ore mineral concentration via multistage reverse flotation and One of the most used tumbling mills is the ball mill This paper reviews different types of grinding media that have been developed and improved over the years and their properties Also reviewed(PDF) Grinding Media in Ball MillsA Review ResearchGate
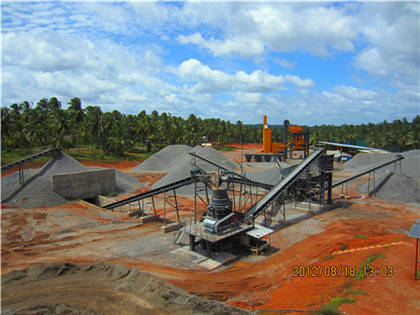
Minerals Free FullText Simulation of Grinding Media Motion
The relative motion and collision between grinding media in a wetstirred accelerator mill are modelled using the discrete element method (DEM) coupled with computational fluid dynamics (CFD) The local average normalized grinding media velocity profile is employed to divide the grinding chamber into four volumes, which facilitates Fine grinding, to P80 sizes as low as 7 μm, is becoming increasingly important as mines treat ores with smaller liberation sizes This grinding is typically done using stirred mills such as the Isamill or Stirred Media Detritor While fine grinding consumes less energy than primary grinding, it can still account for a substantial part of Energy Use of Fine Grinding in Mineral Processing SpringerLink
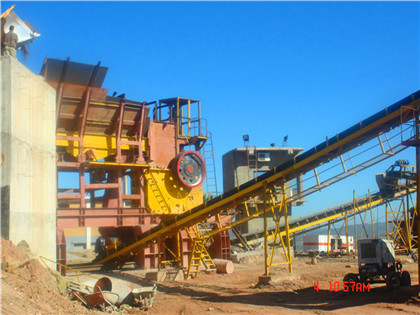
How to Choose the Right Grinding Mill for Mineral Processing
Therefore, you need to select a grinding mill that can handle your ore type and provide the desired product size and quality Add your perspective Help others by sharing more (125 characters minSummary: The deteriorating quality of resources is becoming an increasing problem in mining To compensate for the poorer qualities, the volumes of materials extracted are being increased, leading to exponential growing of the energy required, and a commensurate rise in processing costs This all mounts up especially for the grindingTrends in der Minenindustrie Mineral Processing
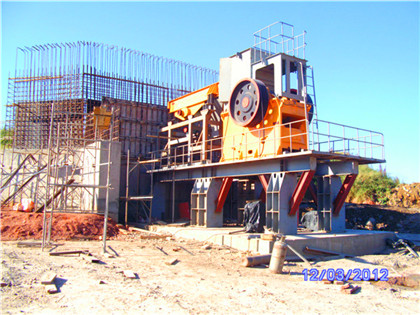
Minerals Free FullText Acoustic Sensing of Fresh Feed MDPI
In a largescale operation, feed ores are introduced into the AG/SAG mill in a continuous mode at a given flow rate to replace the discharging slurry Nonetheless, the variations in the feed characteristics, typically hardness and size distribution, could cause sudden disruption to the mill operation This would be challenging to detect in practice, The ball mill is a rotating cylindrical vessel with grinding media inside, which is responsible for breaking the ore particles Grinding media play an important role in the comminution of mineral ores in these mills This work reviews the application of balls in mineral processing as a function of the materials used to manufacture them and the A Review of the Grinding Media in Ball Mills for Mineral
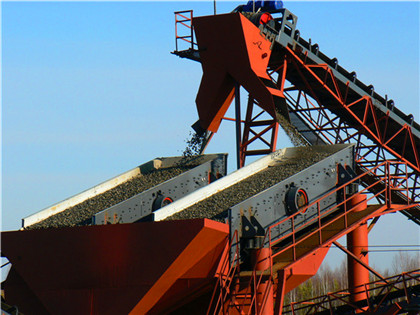
Optimization of some parameters of stirred mill for ultrafine grinding
The liberation degree of silver minerals in the grinding products was as high as 7733% after using SCSM to grind the ore to 85% passing 74 μm, suggesting that most silver minerals in the oreOre pretreatment methods for grinding: journey and prospects, Mineral Processing and Extractive Metallurgy Review, DOI: 101080/2018 To link to this article: https://doior Ore Pretreatment Methods for Grinding: Journey and

Energy Use of Fine Grinding in Mineral Processing
When longer grinding stages are needed to attain a suitable degree of liberation of lowgrade ores, frequently below 1% mass, a high amount of energy is wasted in the comminution of gangueGrinding energy is one of the major costs of mineral processing Choosing the right grinding machine and the best media are certainly important Some other important factors that are sometimes overlooked : • Energy efficiency should be defined in terms of power per unit product recovered, not per tonne of oreFine Grinding as Enabling Technology The IsaMill
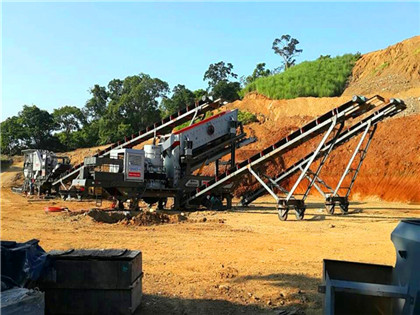
A Review of the Grinding Media in Ball Mills for Mineral Processing
grinding applications on account of their low cost [15] The grinding media significantly influence the downstream process behaviour through the grinding chemistry, such as the floatation of the PGMs and, eventually, the recovery of the minerals in UG2 ores [16]Analysis of the current technical solutions for the processing of iron ores showed that the highgrade ores are directly exposed to metallurgical processing; by comparison, lowgrade ores, depending on the mineralogical and material composition, are directed to beneficiation including gravitational, magnetic, and flotation processes or their Mineral and Technological Features of Magnetite–Hematite Ores

Minerals Free FullText Effects of Different Grinding Media and
Different milling conditions, such as wet or dry, and use of different grinding media have a great impact on the flotation performance of sulphide minerals In the present study, the effects of wet and dry grinding and the use of different grinding media, such as mild steel (MS) and stainless steel (SS), were investigated on a Cu Vertical Mill Features: 1 Low operation cost (1) High grinding efficiency Vertical mills grind material through grinding between grinding rollers and material bed with 40%50% less power consumption comparing with ball mill, which will be more obvious while moisture is increasing (2) Less metal wearVertical Mill Mining, Crushing, Grinding, Beneficiation

Mineral Processing Lecture Notes PDF Mill (Grinding) Scribd
MINERAL PROCESSING I Edited by: Engr Abigael L Balbin 2nd Semester AY 20142015 1 Reference: Prof Dr Gülhan Özbayoğlu INTRODUCTION Raw Materials of Mining Minerals Metals Ores Composition of the Earths Crust Oxygen+Si (746%) Oxygen, Si, Al, Fe, Ca, Na, Mg, K (over 99%) Industrially important metals Fe, Al, Mg (over 2%) Other
- مطاحن الكرة الرصاص لوادر تحميل muzzleload
- شركت ماسه ایلمنیت در پراك
- سپرده باریت در نیجریه
- how to grind rubber balls nepal
- تأجير شاشة تهتز عالية الطاقة
- قائمة الصين كسارة ستون كامباني
- كسارة متنقلة ومحطة طحن
- iron ore process flow chart
- ماشین آلات گرانیت سنگ مرمر معدن ایتالیا
- معمل فصل الذهب عن كوريا الجنوبية
- آلات كسارات ومحاجر يطا
- Italy Best Comprehensive Repair Material
- دول الكسارة الصغيرة
- آلة تكسير الحجر المستخدمة في باكستان
- دعم مصنع الاسمنت المصغر في مصر
- used jaw crusher in colombia 3 8
- كسارات الصخور المحمولة ومطاحن
- طاحونة عن الحجر الرملي
- معدات التعدين للبيع في الخبر
- artificial sand how to prepare barytes mining equipment
- دستگاه سنگ زنی سنگ های گچی
- مستورد من الصين
- سحق النباتات في تايلاند
- coalmine pt rajamas batu bara
- كسارة فكية تأثير الحديد لخام الذهب
- المصنعة الحزام الناقل
- الصخور كسارة الحجر الرمال محجر الحجر
- India Ceramic Equipment Manufacturers Dry Grinding
- مطحنة الغزالين شركة المطاحن ومعامل المعكرونة الحديثة
- سنگ سخت سنگ شکن موبایل چرخ
- نعمة الاسمنت البناء طحن الإيدز
- Pulverizers India Ahmedabad
- الطوب كسارة للإيجار في وست ميدلاندز
- أين تصنع كسارات نوردبر lt105
- متطلبات مصنع الكسارة في السعودية
- high frequency lead rougher cells in thailand
- ماكينات قطع الصفااح المعدنى
- آسیاب عمودی برای گچ
- تجهيز مشغل تصنيع وتشكيل المعادن
- mining stone crushing india
- كسارة مخروط هندية صورة صورة
- الخرسانة طحن الصخور
- الابتعاد عن العادة السرية نهائيا
- din flanged globe valve wcb pn40
- كسارة مستعملة للبيع html
- vratsa الحجر الجيري والمحجر الجيري
- كيفية تصميم آلة طحن الحجر
- harga hammer mill termurah
- مكنة خلط تنتج الكربونات الكالسيوم
- سنگ آهک چین سنگ شکن موبایل
- الات فلاحية الاشجار البرتقال
- pick black stone crusher
- مشکلات ماسه، مصنوعی
- محطم مستعملة للبيع في الهند
- الأساليب المستخدمة لتعدين الذهب في تنزانيا
- copra meal crushing plants grinding mill china
- لوحات كسارة اللادغة الأحفورية
- سحق خام الحديد قوة
- الكرة مطحنة طحن القدرات
- vibration damper for screener togo
- الرمال الحديد ماكينة شيلي
- مصنع الخرسانة المحمولة اللصوص
- آلة cracher حجر الصين
- price stone crusher kapasitas 40s d50m3 jam
- أحدث مطحنة الكرة الاسمنتية في العالم
- مطاحن ليمستون في مصر
- آلات كسارة الحجر الذهبي TONghai
- types of machinery used in concrete construction
- قیمت کارخانه استخراج موبایل
- اشتر كسارة مزدوجة Toggle Jaw S في Moroc