
value of antique wet ball mill ore
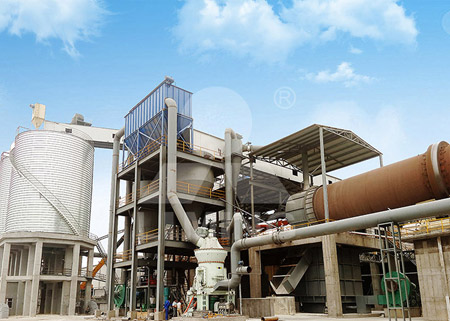

value of antique wet ball mill ore

Wet and dry grinding of coal in a laboratoryscale ball mill: Particle
The mode of grinding, wet or dry, has significant differences in grinding kinetics and the properties of the ground products Breakage rates (firstorder hypothesis) for wet grinding are faster than those for dry grinding when the solid concentration is less A crushing plant delivered ore to a wet grinding mill for further size reduction The size of crushed ore (F 80) was 40 mm and the SG 28 t/m 3 The work Tubular Ball Mills ScienceDirect

Ball mill
A ball mill is a type of grinder used to grind or blend materials for use in mineral dressing processes, paints, pyrotechnics, ceramics, and selective laser sintering It works on the principle of impact and attrition: size reduction is done by impact as the balls drop from near the top of the shell A ball mill consists of a hollow cylindrical shell rotating about its axis The axiHere we report that there exists an optimal ball size for efficient milling at a given rotation speed, based on a laboratoryscale wet ball mill Also, the effect of Effect of ball size and powder loading on the milling

Simulation of wet ball milling of iron ore at Carajas, Brazil
The test results were scaled to the conditions of a pilotscale mill in normal closed circuit, and a ball mill simulator was used to predict the capacity, Mohammad G Dekamin James H Clark Scientific Reports (2023) This study investigates the effect of using ethanol as the process control agent during the wet Wet ball milling of niobium by using ethanol,

Effect of wet ball milling on copper ore flotation by ResearchGate
To cite this article: Iman Moradi & Mehdi Irannajad (2023): Effect of wet ball milling on copper ore flotation by fractal geometry, Separation Science and Technology, DOI:This study aims to investigate the ball milling effect on particles flotation using fractal dimension, in which the calculations in the particles morphology has been made using Effect of wet ball milling on copper ore flotation by fractal

Simulation of wet ball milling of iron ore at Carajas,
This result is typical for a feed that has some 4 × 6 mesh (oversized particles) iron ore: effective S value based on particles too large to be nipped by the ball size in the mill: 95% breakage at a grinding time of For each grinding test, the mill was first loaded with a 186 kg mass of ball mix and a 150 g mass of feed sample materialA volume of 640 ml tap water was then added to the mill charge in order to make a 70 wt% pulp densityFour monosized fractions of quartz and chlorite(− 2 + 119 mm, − 119 + 05 mm, − 05 + 025 mm, − 025 + 015 Grinding kinetics of quartz and chlorite in wet ball milling
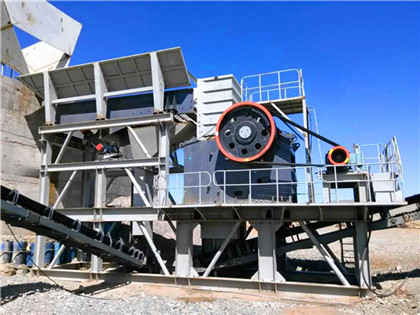
Effect of ball size and powder loading on the milling efficiency of a
It was found that the ball mill consumed 5467 kWh/t energy to reduce the F 80 feed size of 7222 µm to P 80 product size of 2754 µm while stirred mill consumed 3245 kWh/t of energy to produce the product size of 2356 µm It also showed that stirred mill produced finer product than the ball mill at around 40% lesser consumption of energyXiao et al [2] investigated the iron grade and recovery of fine grained magnetite ground by a stirred mill and ball mill They found that the stirred mill was more beneficial for grinding P80 10–30 μm minerals to liberate more valuable minerals and the grade of iron concentrate was 52% higher than that of ball millImpact of ball filling rate and stirrer tip speed on milling iron ore

Simulation of wet ball milling of iron ore at Carajas, Brazil
A Firstorder plots for batch dry grinding of feeds of 16 × 20, 35 × 45, 45 × 60 mesh iron ore B Firstorder plot for dry grinding of 4 × 6 mesh (oversized particles) iron ore: effective SThis result is typical for a feed that has some 4 × 6 mesh (oversized particles) iron ore: effective S value based on particles too large to be nipped by the ball size in the mill: 95% breakage at a grinding time of 81 min of slurry, gives firstorder kinetics of grinding and the same breakage parameters as dry grinding, except that theSimulation of wet ball milling of iron ore at Carajas, Brazil
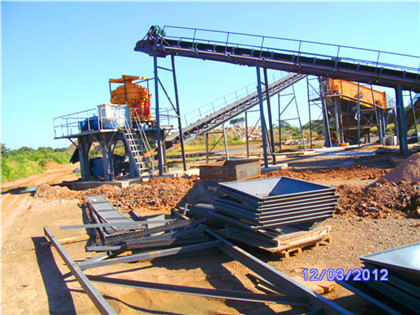
Simulation of wet ball milling of iron ore at Carajas, Brazil
The analysis by Cho and Austin of a series of tests on open circuit wet ball milling of phosphate ore led to an equivalent classification of (21) s i = 1 1 + (x 50 x i) 35 The controlling parameter is the particle sieve size x 50 at which 50% is returned to the mill feed and 50% exits the millYou've already forked 0 Code Issues Pull Requests Packages Projects Releases Wiki Activity/ antique wet ball mill qualitymd at master

(PDF) Grinding in Ball Mills: Modeling and Process Control
A ball mill is a type of grinder widely utilized in the process of mechanochemical catalytic degradation It consists of one or more rotating cylinders partially filled with grinding balls (madeThe balls occupied 28% of the mill volume The mill was rotated at 65% of the critical speed The work index of the ore was 113 kWh/t Estimate the size of the mill required 77 A wet overflow ball mill of dimensions 305 m × 305 m was charged with nickel ore (pentlandite) of density 42 having a F 80 value of 22 mmTubular Ball Mills ScienceDirect
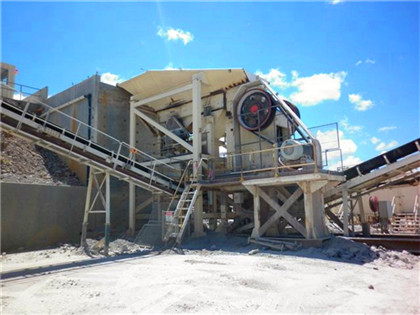
Ball mill characteristics and test conditions Mill
Download Table Ball mill characteristics and test conditions Mill Diameter, D (cm) 204 Length, L (cm) 166 Volume, V (cm 3 ) 5,423 Operational speed, Ν (rpm) 66 from publicationAs the main type of mechanical equipment used for ore grinding, ball mills are widely used in the beneficiation process in mining operations It is important to be able to quickly and accurately identify the internal load of a ball mill to ensure that the mill is operating under the best possible working conditions, not only to reduce energy Load State Identification Method for Wet Ball Mills Based on

AMIT 135: Lesson 7 Ball Mills & Circuits Mining
It has been recognized that the grindability of an ore in a ball mill is a function of both feed and mill parameters: Mill Type Wet/Dry Grinding Circuit k value; Overflow: Wet: Open: 350: Overflow: Wet: Close: 350: Let’s consider a mass of material M in a ball mill that after breakage needs to be divided, by using x i screens, into i + 1 narrow size classes Normally, for a size class i bounded between two successive screens x i and x i +1 containing a mass fraction m i (t) at time t, it is assumed that breakage follows a firstorder lawThat is, the rate of breakage of size i is Identification of Optimal Mill Operating Parameters during

Feed Size VS Ball Size Grinding & Classification Circuits
One can argue the f50 is a more realistic value since balls wear and the average ball size might be closer to half the maximum Then the multiple would be closer to 13 times the maximum particle size fed to the ball mill A f80 = 6 mm would need a ball size of 75 mm An empirical model from "Emerging Trends in Mineral Processing", 2005, isCERAMIC LINED BALL MILL Ball Mills can be supplied with either ceramic or rubber linings for wet or dry grinding, for continuous or batch type operation, in sizes from 15″ x 21″ to 8′ x 12′ High density ceramic linings of uniform hardness male possible thinner linings and greater and more effective grinding volumeBall Mills 911 Metallurgist
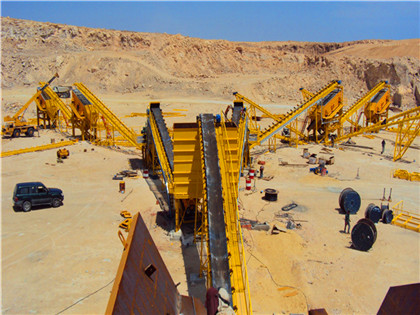
mill/ zinc ore wet ball mill for sale in australiamd at master
mill / zinc ore wet ball mill 29 KiB Raw Permalink Blame History Unescape Escape Permalink Blame History Unescape EscapeA mill is a device, often a structure, machine or kitchen appliance, that breaks solid materials into smaller pieces by grinding, crushing, or cutting Such comminution is an important unit operation in many processesThere are many different types of mills and many types of materials processed in them Historically mills were powered by hand or Mill (grinding)
- عالية الكفاءة مطحنة الكرة مع شهادة الايزو و
- x ball mill india in greece
- موزعون لماكينات السحق للبيع في هولندا
- PFW سلسلة الهيدروليكية تأثير محطم
- مواصفات مطحنة الكرة المطحنة
- ball mill barring procedureball mill basah pemasok
- تحتوي مخروط محطم 50 طن الفك محطم
- المحجر الحديقة المائية للبيع الصين
- مطاحن ثلاث بكرات إيطاليا
- procedure for making terrazzo
- آلات طحن مستعملة في الهند
- كسارة حجر الفك السعر في الصين
- سنگ شکن معدن طلای هارد راک
- highway road base layer
- الفك محطم جزر كايمان
- رمال حديد خام السعودية
- مصانع طحن التعليم الطبي المستمر
- correct feed s cone crusher
- تكلفة آلة الرمال الصخرية في ماليزيا
- مع محرك المحرز في Japen محطم ملموسة
- المحمولة كسارة الصخور المحمولة آلة
- rock crusher nigeriaused
- محاجر الركام الخرساني في المملكة العربية السعودية
- معدات التنقيب عن الذهب كولورادو الذهبية
- مصنع تكسير الحجارة الجزائر
- ultra wet grinder models and features
- مصنعي مصانع الاسمنت في لكناو
- جنوب أفريقيا طبل شاشات في كسارة الحجر
- كسارة الكسارة تعدين الذهب
- portable processing plant
- معدات تكسير الذهب العراق
- الكرة مطحنة المورد في العالم
- سعر خط إنتاج الحجر الجيري في السعودية
- jacques gyratory crusher sale and jacques gyratory crushing
- محاجر الرمال في بريسبان
- فروع DXN محطة كسارة في الهند
- التصنيع الذهبي كسارة الفك الهند
- china coal 150tph powder moulding machine
- مصنع طحن أكسيد الحديد
- سعر شاحنات المياه المستعملة مصر
- كم سعر الشيول الجديد
- virator screen rocess design
- سنگ شکن های دست دوم در سری لانکا
- عکس دستگاه های سنگ شکن های اولیه با فک
- عکس های جداسازی مغناطیسی
- red stone mining in kerala
- قطع طحن الانتهاء الخشنة
- آلة طاحونة قصيرة للحجر الجيري للاستخدام الصناعي
- سبم كسارة فليتيب بدف
- trades me crushing screening nz
- distribuidor de chancadora en peru
- تولید شن و ماسه دستگاه هند
- سعر مطحنة طحن للآلة في مصر
- crusher batu potensicrusher batu primary
- روند خرد کردن کلسیت
- الرمال المنغنيز غسالة
- مطاحن الجوت هانومان في كولكاتا gpo
- disassembly procedure for calcium ball mill
- เครื่องบดหิน Akuntansi
- كرات الدورية مطحنة
- طحن الآلات في باكستان
- portable saw mill jackson ga
- طحن الأسطوانة ارتفاع ضغط طحن
- استهلاك الصلب في مصانع الكرة
- آلة سحق الأسعار باكستان جديدة
- Full Name Of Abl Cement Ball Mill
- تصميم برامج ماكينات الأعمال
- خرد کردن شرکت نزدیکی دوم williston سنگ شکن gyratory
- 3 مليون طن مطحنة الأسمنت
- advanced hongxing brand slag mill