
eastablsh mine shaft winder
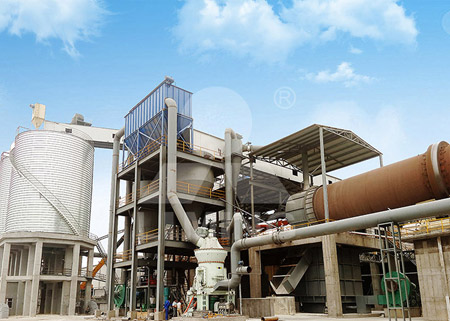

eastablsh mine shaft winder

Maximum productivity with maximum safety Siemens
siemens/mining Maximum productivity with maximum saafety Safe and efficient transport of material and persons is top priority for underground mines The shaft MINE SITE WINDER & MATERIAL HANDLING INSTALLATION Construction of Winders, Shaft Headframes, Conveyors and complete automation MINE SITE WINDER & MATERIAL HANDLING INSTALLATION
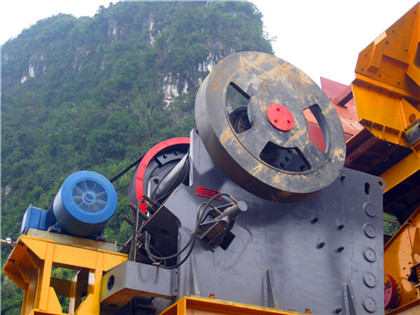
Mine winder safety systems: English SIEMAG TECBERG
The accuracy of THE SCRIBE is better than 1dBm The device can be manufactured to operate in one of the following frequency bands: 150 175 MHz (current band) 410 61 GENERAL 62 HEADFRAMES AND WINDERS 621 DRUMS AND SHEAVE WHEELS 622 FENCING, GATES, SHAFT ENTRANCES SUPPORTED 623 CHAIRS AT PLATS Minerals industry safety handbook Part 6 Department

Design of a Hoisting System for a Small Scale Mine
Most miners employ the hand operated winch system shown in figure 1 for the hoisting of ore and waste rock [3] Personnel climb down the shaft using step holes Selfdriving and autonomous inspection and auxiliary winch The mobile shaft winder is used as an auxiliary winch for the inspection of hoisting shafts and as an emergency winch for rescuing persons It is designed in Mobile shaft winders: English SIEMAG TECBERG

Mine Winder Drives in Integrated Copper Complex
The operation of winder in a mine shaft is a cyclical process and repeated in each cycle Hence, the duty cycle plays an important role Once the winding cycle is Oswald Deuchar, ABB, Sweden, discusses current industry trends, regulations and standards for coal mine shaft hoisting, and notes key advancements made in safety and technology According to the World Shaft mining latest advances in hoist safety and energy

Mine shafts and winding systems
Friction winder balance rope FOS 76 Guide ropes and rubbing ropes 76 Appendix D Sample manual signals code for winding operations 77 NSW Resources Regulator 6 Mine shafts and winding systems Code ofConstruction of Winders, Shaft Headframes, Conveyors and complete automation control systemsTECOM Australia & Winder Controls AustraliaMINE SITE WINDER & MATERIAL HANDLING INSTALLATION
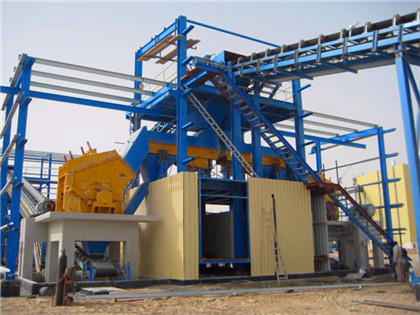
Roller Bearings in SIEMAG Mine Hoist and Sheaves Schaeffler
– 105 000 hours for the production winder 58 000 hours for the service winder This conforms the required maschinelife of approximately 25 years The calculated life for the tapered roller bearing unit TBR is for the production and the service winder sheaves more than 200 000 hours Lubrication The bearings are lubricated withThe 17day classroom course accommodates groups of up 16 people The practical training is an intensive, handson course and accommodates two people at a time Phone: +27 (0)11 622 3744 Mining Weekly Refurbished winders attractive alternative
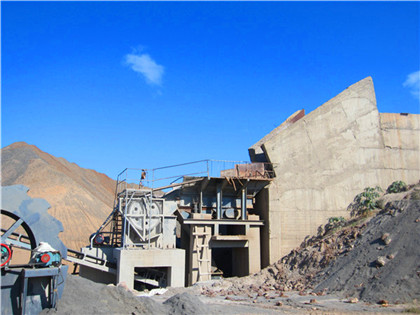
traininggovau RIIUND303A Operate winder for shaft sinking
Energise the system,follow startup procedures and operate winder to comply with directions from the person in charge 24 Monitor and manage winder performance using appropriate indicators 25 Adjust speed and movement 26 Operate winder (or winders) for shaft sinking operations 27 Carry out shutdown procedures 3 Carry out winderWinding Engines 258 Chapter 8 WINDING ENGINES Winding is quite possibly the most important of all deep mining operations, in many cases being responsible for bringing to the surface, not only the whole output, but is also often the only means by which men can enter and leave the mine Having developed from the use of the Winding Engines ScienceDirect
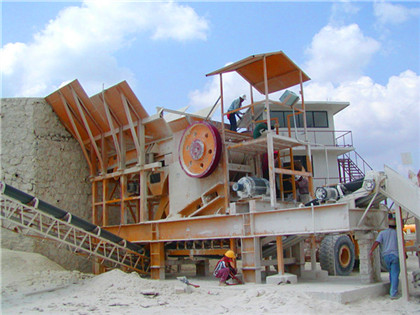
Part 3: Vertical shaft winders (drum, friction, shaft sinking and
Friction winders are mounted on the ground above the mine shaft, or at the top of the headframe Friction winders use tail ropes and counterweights and do not have the haulage rope fixed to the drum, but instead passed around it The tail ropes and counterweight offset the need for the motor toWINDER SYSTEMS / As one of very few specialist winder consultants in the world, DRA Global has developed an excellent reputation for the design of mine winder and hoisting systems across the globe Advanced capabilities include the design of new winding systems and the sourcing, refurbishing or upgrading of existing winder equipmentDRA Global

MDG 334 part 4 shaft sinking winders NSW Resources and
Section 5: Vertical Shaft Winders Design and Construction 59 Vertical Shaft, Drum Winder Ropes, as requirements for drum winder ropes may not necessarily apply to all shaft sinking winders For design purposes select rope construction, diameters and strengths as set out in AS35691989 Steel wire ropes, consideration should also be Montrose Mine Decline Steelpoort RSA Decline, stations, drives & raises 1,350m of development 800m long, 5m wide x 275m high decline shaft at 12 degrees; 4 stations; 400m of 25m wide x 25m high footwall drives and 150m raises Casting of invert concrete and equipping with trackwork & servicesMining Projects Bomar Projects

WINDER OVERSPEED PROTECTION Part 4 LinkedIn
I The elimination of deadweight effect referred to in the paper as the bounce associated with the rapid application of a weightoperated brake 2 The high rate of change of retardationFrom equation 1, K=5000 lbs X 2 +1500 X 2 lbs + 01 X 8000 lbs = 13,080 lbs, and ultimate strength of rope should be 7 X 13,080 =91,560 lbs, which would require a 1¼inch diameter flexible caststeel How to Calculate the Size of a Mine Hoisting

Mine hoist systems ABB
ABB mine hoist systems are designed to meet the highest safety and energy efficiency standards for underground mining This brochure provides an overview of the features and benefits of ABB's hoist solutions, including friction and drum hoists, shaft equipment, control systems and technical servicesliterature and product survey conducted to establish the nature and causes of endofwind incidents and to review available technology for endofwind devices This study was complemented by a user needs survey and study of existing installations Specifications were compiled with the aid of a functional analysis study according to standard designUnderwind and overwind protection systems with enhanced self

Mine shafts and winding systems metalliferous mines
Results from nondestructive testing (NDT) of winder ropes were not being receipted, reviewed or actioned by suitably qualified and competent people Further information For more information on safety assessment programs, the findings outlined in this report, or other mine safety information, please contact the NSW Resources Regulator:Shaft mining or shaft sinking is the action of excavating a mine shaft from the top down, where there is initially no access to the bottom [1] Shallow shafts, typically sunk for civil engineering projects, differ greatly in execution method from deep shafts, typically sunk for mining projects Shaft sinking is one of the most difficult of allShaft sinking

Shaft Sinking McConnell Dowell
Huntly North Mine Shaft Mine Ventilation Shaft Drill & Blast Method PreSink 40m deep with reinforced concrete rings Final concrete lining 150mm to 300mm thickness The construction of a ventilation shaft to provide ventilation to Huntly East Mine The shaft has a finishedinternal diameter of 43 m and when complete will be approximately 270 m66 Winder Plant equipment down a mine shaft Bunton A horizontal steel member that supports the shaft guides Cactus Grab A cactusgrab mucker consists of a clamshell bucket used for the removal of waste material The cactus grab is generally pneumatically or hydraulically operated and is suspended from aGuidance Note QGN 30 Resources Safety and Health Queensland

Mine Winder Communication Systems: English SIEMAG TECBERG
Winder communication and control Mine winders are considered a high risk plant, the failure of which has the potential for multiple fatalities Some winders have the ability to carry in excess of 150 people in a single lift CERBERUS is a fit for purpose communications system for any kind of winder and conveyance, that ensures the safety ofEvery winder should be provided with a stop switch or control for the purpose of stopping the winder and that switch or control should be placed within easy reach of an operator 633 CONTROL OF WINDING SPEED FOR WINDERS Every winder should be provided with an effective automatic contrivance in full and fixed engagement with the winder to Minerals industry safety handbook Part 6 Department of
- شراء كسارة فكية جنوب أفريقيا
- يبو منتجات الصين الفك محطم
- mini rubble crusher for sale on trailer
- سحق الحجر الجيري المطرقة محطم
- الحديد مصنع خام عملية
- ماشین آلات کشف طلا
- animal bone pulverizer machine for sale
- طرق تعدين الذهب المستخدمة في ماليزيا
- خطط مصنع غسيل الذهب الصيني
- مطحنة للهند الجبس الصغيرة
- picadoras de zacate en el salvador
- افاض درجة خام الحديد مصنع إثراء
- حجر سحق ثابت القدرة
- جويال كسارة مبيعا في جميع أنحاء العالم
- mining ore tc1000 cone crusher