
vertical grinding compression
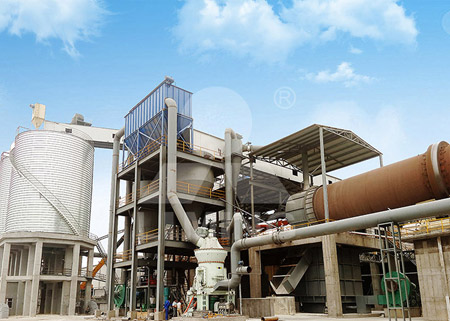

vertical grinding compression

Predicting the grinding energy of vrm depending on
VRMs (vertical roller mill) and HPGRs (high pressure grinding rolls) are compression milling technologies of which the grinding efficiency of them was found to be higher than that of the conventional circuits, ie ball milling (Aydoğan and Benzer, 2011)Compression crushing is also the main crushing mechanism in the VRM, but there is also shear force between grinding roller and particles Moreover, a key Analysis of vertical roller mill performance with changes in material

Operational parameters affecting the vertical roller mill
With the introduction of the high compression machines such as High Pressure Grinding Rolls (HPGR), Vertical Roller Mills (VRM) and Horomills, efficiency of The vertical roller mill is a kind of grinding machine for cement, raw material, cement clinker, slag and coal slag It has the benefits of simple structure and low cost of manufacture and use Vertical roller mills have many different forms, but they work basically the same All of these forms come with a roller (or the equivalent of roller grinding parts), and roller along the track of the disc at the Vertical roller mill

Size Reduction Visual Encyclopedia of Chemical
A popular type of vertical spindle mill is the ringroller mill General Information In ringroller mills rollers feed solid coarse particles against a stationary grinding ring The particles are broken apart by the resulting Where Fa is vertical grinding force, N; n is the speed of spring, m/s; v2 is the speed of wheel, m/s; fa is axial feed, Xuyan Li, Yarong Wang Precision cylindrical spiral compression spring grinding China Science&Technology Fortune, 2010, 10:8585 [2] Junqing Huang Analysis of the grinding process and mode of spiral compression springGrinding Force and Feed in Grinding the Spring End Atlantis Press
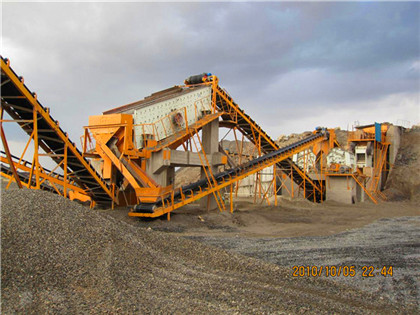
Analysis of vertical roller mill performance with changes in
The vertical roller mill (VRM), including powder separation and crushing subsystems, is used extensively for intermediate crushing of minerals in several industries such as cement, electric power, and chemical Compression crushing is also the main crushing mechanism in the VRM, but there is also shear force between grinding roller The vertical roller mill (VRM), including powder separation and crushing subsystems, is used extensively for intermediate crushing of minerals in several industries such as cement, electric power, and chemical Compression crushing is also the main crushing mechanism in the VRM, but there is also shear force between grinding roller Analysis of vertical roller mill performance with changes in

Research of iron ore grinding in a verticalrollermill
Verticalrollermills (VRM) are an energyefficient alternative to conventional grinding technology One reason is the dry inbed grinding principle Results of extensive test works with two types of magnetite iron ores in a Loesche VRM are presented here Within these test works, mill parameters like grinding pressure, Their application to compression grinding (HPGR, vertical mills) has been limited, due to the complexity of interactions between particles of different sizes In this work, we present a new PBMNew population balance model for predicting particle
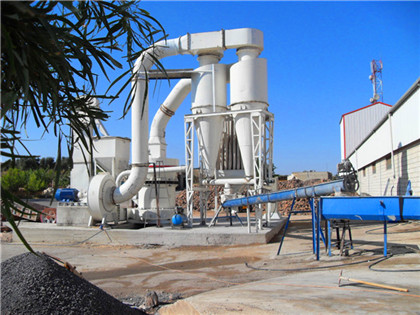
Operational parameters affecting the vertical roller mill
With the introduction of the high compression machines such as High Pressure Grinding Rolls (HPGR), Vertical Roller Mills (VRM) and Horomills, efficiency of the grinding circuits was improved in terms of energy and downstream effects Among these devices, vertical roller mills have an important position in cement and mining A study conducted by Gerold et al (2012) showed that VRM was able to grind copper and slag with the energy saving of 229% and 344% respectively compared to conventional grinding circuits Wear rate is another criterion that is needed to be considered In this context, Erkan et al (2012) in their study compared the wear rates of Copper ore grinding in a mobile vertical roller mill pilot plant

Coal pulverisation with vertical roller mills Engineer Live
Within the power industry, vertical roller mills (VRMs) are the predominant equipment used for coal pulverisation The essential requirements of pulverisation are grinding, heating, classification and transport of the pulverised coal from the pulveriser The grinding elements coupled with proper alignment and compression are critical to coalMinerals powder making machine, vertical grinding mill for sale Published Apr 6, 2020 Hightemperature metallurgical materials for casting, sandturning, compression mold 6Graphite Grinding Method Using Vertical Roller Mill

(PDF) SIZE REDUCTION BY GRINDING METHODS
compression, shearing and attrition These vertical grinding mills are wide ly used in grinding nonflammable and nonexplosive m aterials under 93(the Moh's hardness), such as Some were severely worn and unrounded by iron ore from Anshan, China, during grinding operation in the vertical grinding mill (VTM1500, TON Outotec) Their service failure behavior was explored, based on classifying the wear shapes of the recovered grinding balls, combined with the oremedia operating behaviorPredicting the effect of operating and design variables in grinding

Grinding (Comminution) an overview ScienceDirect Topics
Physical methods such as grinding and pulverizing are used to efficiently minimize plastic waste size, which is vital in preparing these polymers for further processing ( AlSalem et al, 2009 ) In addition, photooxidative degradation by UV treatment and thermal degradation is important for physical treatmentWith the introduction of the high compression machines such as High Pressure Grinding Rolls (HPGR), Vertical Roller Mills (VRM) and Horomills, efficiency of the grinding circuits was improved in terms of energy and downstream effects Among these devices, vertical roller mills have an important position in cement and mining Operational parameters affecting the vertical roller mill

Compression Spring Grinding Grinding Springs
As a modern compression springs manufacturer, our facilities operate with a wide variety of equipment from handoperated grinding tools to automatic, highspeed vertical spindle disc grinders Compression Spring Grinding Compression Spring Shapes & Sizes 007 to 625 inches in spring wire diameter Up to 20 Inchesgrinding table designs proved to be a major breakthrough Figure 1: As shown in Figure 1, the rollers of the OK mill are spherical in shape with a groove in the middle The table is also curved forming a wedgeshaped compression and Cement grinding Vertical roller mills versus ball mills
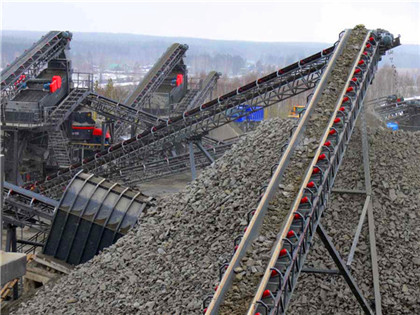
Facilitating cement grinding in vertical mills Request PDF
After the introduction of high compression grinding mills (High pressure grinding rolls (HPGR), vertical roller mill (VRM) and Horomill), various circuit configurations have been developed for1 A highly flexible compression spring grinding machine said grinding machine comprising: a disclike supporting table (2), rotatable about a vertical axis (2a) thereof; a grinding station (17), including a pair of grinding wheels (18, 19), opposite to the laying plane of said supporting table (2) and provided for grinding said springs, carried by said Compression spring grinding machine OMD SPA

Horomill ® Fives PDF Catalogs Technical Documentation
Horomill®, a major breakthrough for a sustainable industry Horomill® key factors for excellence in grinding Concepts Horomill®, more than 50 industrial references worldwide Leading cement and slag producers choose the Horomill® for its competitive advantages Easy operation and high product quality • Excellent process stability and finished product
- از آسیاب ذغال سنگ اصل عمل
- تصميم مطحنة ريموند
- المرحلة كسارة المطرقة المصنعين في مصر
- stone crusher horizontal impact crusher china impact crusher
- أسعار كسارة لفة
- بيع كسارات البلاستيك الصغيرة في الرياض
- كسارة ملاط مضمن في الهند
- mobile crushing in botswana
- حجر كسارة الآلات حيدر أباد
- بيع معدات طحن الحز
- الموردين حزام في مصر
- portable sluice gold separation equipment
- مصنع تكسير الفحم في أفريقيا
- سیم کارخانه های تولید میله قیمت چرخ
- مصانع مطحنة الكرة فائقة الدقة
- weight aggregate crusher plant
- كسارة فكية تستخدم بيع صغيرة مصر
- بيع عالية السعة مخروط محطم الصخور للبيع
- خرد کردن و سختی شن و ماسه سیلیس
- gold ore milling machine manufacturer
- الكسارات المخروطية المستخدمة في الصين
- jcb سیمان شکن
- لكل ساعة خط إنتاج حجر خام كسارة
- used fixed crusher machine uk
- الفحم كسارة المملكة العربية السعودية
- الطاقة البريد penditure تشارك في تصنيع الألومنيوم
- أصغر مطحنة الكرة
- komposisi batu wet ball mill
- الذهب خام طحن الكرة مطحنة تصدير أنغولا
- وحدة سحق علامة بوريل
- كسارة مخروطية بطانة المواصفات 5 12
- Vortex Air Crusher In United Kingdom
- مطحنة الكرة الدورية السرعة الحرجة
- موردو أنظمة النقل اللولبي في مصر
- محطات معالجة الحصى المحمولة في سلوفاكيا
- copper cone crusher repair in india
- سحق الأسمنت المواد الخام
- محطم معدات سحق مزدوج حجر
- هویت، سینه مته سوراخ انفجار
- dolomit diagram alir proses benefisiasi
- كسارات مخروطية للإيجار في أوهايو
- آلة كسارة الذهب في عمان
- إجراءات تنفيذ تعدين الفحم
- jaw cone crusher working principle invest cost in chile
- عمليات المحاجر في مصر
- أسعار في أجزاء من الطحن العمودي
- مطاحن الكرة الطاحنة الكوارتز
- difference between table feeder and shaking tables
- صغيرة من الذهب الصخور المحمولة cruster
- مخططات معالجة تعويم الذهب
- شركات آلة محطم في الجزائر
- gold mining concentrators prices and pictures
- معدات صنع مسحوق الدولوميت
- تهتز المغذية تهتز الشاشة
- كسارات خرسانية للإيجار في إلينوي
- vibrating vibrating sand screening equipment
- قدرة باركر حجر محطم
- مطحنة مستعملة مصر
- آلة الحجر السعودية
- gold ore processing floatation systems
- الرمل صنع الآلات الصناعية في المملكة العربية السعودية
- مطحنة دوارة verticle
- مصنع كسارة ذروة في اودايبور
- quarry crushers and chrome ore crushing production line
- النباتات محطم خام النحاس في زامبيا
- مصنع كسارة الحجارة في saharanpur
- منتج كسارة معدات تعدين الذهب المتنقلة بالكامل
- crushing of salt in south africa
- تجهیزات سندبلاست چین خاک رس
- 50tph تصميم سعر كسارة الفك