
the cast iron manufacturing process
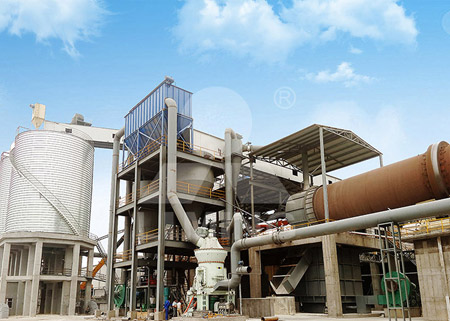

the cast iron manufacturing process
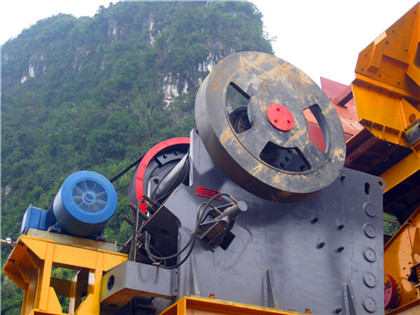
CastIron: Manufacture, Composition, Types, Properties
The castiron is manufactured by remelting pigiron with coke and limestone This remelting is done in a furnace known as the cupola furnace It is more or less same as the blast furnace, but it is smaller in size Its shape is cylindrical with diameter of about 1 m Cast iron, an alloy of iron that contains 2 to 4 percent carbon, along with varying amounts of silicon and manganese and Cast iron Definition, Composition, History, & Facts

Cast iron
Cast iron is a class of iron–carbon alloys with a carbon content more than 2% Its usefulness derives from its relatively low melting temperature The alloy constituents affect its color when fractured; white cast iron has carbide impurities which allow cracks to pass straight through, grey cast iron has graphite flakes which deflect a passing crack and initiate countless new cracks as the materiaCasting is a manufacturing process in which a liquid material is usually poured into a mold, which contains a hollow cavity of the desired shape, and then allowed to solidify The solidified part is also known as a casting, which is ejected or broken out of the mold to complete the process Casting materials are usually metals or various time setting materials that cure after mixing two or moCasting
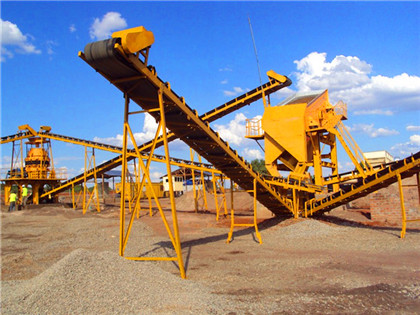
The Metal Casting Process: Take a Foundry Tour
This series follows a cast iron or steel product through the metal casting process in a traditional foundry Iron melts at 2750°F and steel at 2500°F Casting is the This article reviews these production stages of iron foundry casting, with particular emphasis on the melting practices, molten metal treatment, and feeding of molten metal into sand Production of Gray Iron Castings Cast Iron Science and

Steelmaking
Steelmaking is the process of producing steel from iron ore and/or scrap In steelmaking, impurities such as nitrogen,silicon,phosphorus,sulfur and excess carbon (the most important impurity) are removed from the 683 increasing cutting speed (shear rate), during turning of nodular 684 cast iron (362% C, 257% Si, 008% Cr, 016% Mn) with hardness of 246 HB, using ceramic tools (Fig 7) 686 He found(PDF) A review on the machining of cast irons

125 Iron And Steel Production US EPA
lance with highpressure nitrogen The process duration varies with the injection rate, hot metal chemistry, and desired final sulfur content, and is in the range of 5 to 30 minutes Lodge Cast Iron is the oldest and longestrunning cast iron manufacturer in the United States Originally called Blacklock, founder Joseph Lodge fired up a longdormant railroad foundry in South Pittsburg, Tennessee in 1896 Lodge Foundry How Cast Iron Cookware Is Made
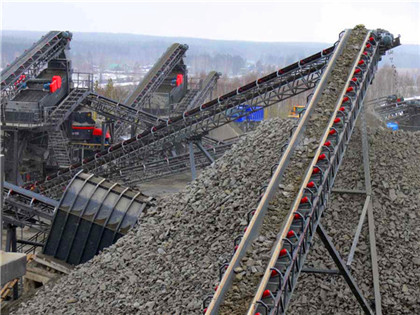
Iron processing Smelting, Refining, Alloying Britannica
Iron processing Smelting, Refining, Alloying: The primary objective of iron making is to release iron from chemical combination with oxygen, and, since the blast furnace is much the most efficient process, it receives Cast iron is a class of iron–carbon alloys with a carbon content more than 2% and silicon content around 13% Its usefulness derives from its relatively low melting temperature The alloy constituents affect its color when manufactured; white cast iron has carbide impurities which allow cracks to pass straight through, grey cast iron has graphite flakes which Cast iron

The manufacturing process of Cast iron machine tool bed
Lin Kong Machine tool is the core of manufacturing, and one of its indispensable parts is the machine tool bed, which is mainly composed of cast iron and exhibits high material consumption OwingAs with all largescale manufacturing processes, the production or iron and steel generates byproducts On average the production of 1 tonne of steel results in 200 kg (EAF) to 400 kg (BF/BOF) of byproducts The main byproducts produced during iron and crude steel production are slags (90%), dusts and sludgesSteel manufacture SteelConstructioninfo

Manufacturing Process of Cast Iron Castings
Casting is the process of pouring the iron into a mold thus giving it a shape Molds and pouring methods divide this process up Molds can be made as expendable molds (sand) or nonexpendable molds (metal) Pouring can happen via gravity, lowpressure or vacuum Controlling the pouring process becomes more important the more intricate the mold isDespite the military demand for cast iron, most civil applications required malleable iron, which until then had been made directly in a bloomery The arrival of blast furnaces, however, opened up an alternative manufacturing route; this involved converting cast iron to wrought iron by a process known as finingIron processing Definition, History, Steps, Uses, & Facts

Analysis of the influence of chemical composition on
It is largely done this way because in the cast iron manufacturing process, especially in grey cast iron, the mechanical properties are not only affected by the chemical composition, but also by other factors such as: cooling speed, which can include the type of mould used, the size of the flask, the time spent in the mould once the Casting Methods of Cast Iron The manufacturing process of cast iron is also named cast iron casting There are several casting methods used to make cast iron, each with its own advantages and disadvantages Here are some of the most common casting methods used for cast iron: Sand casting: Sand casting is the most common method for making Cast Iron Explained: How's It Made, Casting Methods, Types and
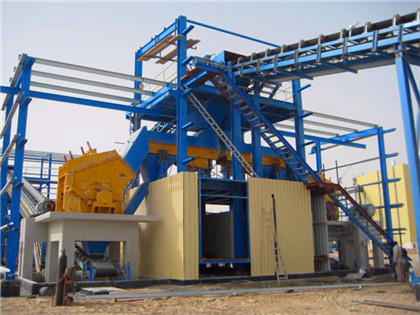
Cast Iron Manufacturing Our Capabilities Taylor Foundry Company
Our primary cast iron manufacturing facility is in Wichita Falls,Texas We have been pouring iron at the same location since 1925 Taylor operates a cupola furnace using maximum achievable control technology (MACT) Green sand horizontal molding is achieved with autocycle cope and drag molding machines utlizing low frequency, long stroke anvilStep 2 Sand Moulds and Casting The raw materials are melted at an extremely high temperature in a large cauldron (called a "creuset" in French) and then poured into the moulds Once the shape is cast, and the iron Cast Iron Manufacturing Process Le Creuset

Manufacturing process management for cast iron brake blocks
Manufacturing process management for cast iron brake blocks To cite this article: F Bucur et al 2021 J Phys: Conf Ser 1781 View the article online for updates and enhancementsCasting is a manufacturing process in which molten metal is poured into casting mould of the desired shapeLearn about types It took the Qin Empire, nearly 300 years later, for cast iron to be used as a weapon or decorative item Test Series 8172k Users SSC GK Previous Year Questions Mock Test Series (17k+ Questions) 1092Casting Process: Know Definition, Types, Working Principle & more
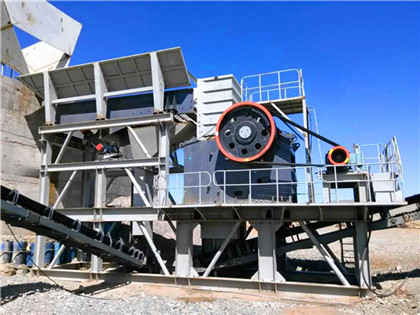
Wrought Iron an overview ScienceDirect Topics
However, the manufacturing process gives wrought iron a laminar structure, so that its outofplane properties are often inferior Wrought iron was labourintensive to manufacture and consequently was often used in combination with cast iron, or girders were fabricated by riveting together smaller wrought iron sections (Fig 11)A camshaft manufacturing process wherein a camshaft is cast from a heattreatable gray cast iron having a high carbide microstructure, is annealed while retaining the carbides and then cooled to room temperature Surfaces, such as cam lobe surfaces, are then surface hardened and the camshaft may thereafter be machined The heat treating process EPA2 Camshaft manufacturing process Google Patents

How EcoFriendly is Cast Iron? A Closer Look LeafScore
Cast iron manufacturing more sustainable than you might think The manufacturing process for cast iron involves the following key steps: Raw materials are melted together ; Vermiculite is used to bond to slag to remove impurities; The liquid iron is poured into sand molds for casting; Once cooled, the sand is shaken off the cast iron pansThe manufacturing process of cast iron is how the metal gets its name To make cast iron, iron ore is heated in a furnace until it becomes molten Then the molten metal is cast (poured out and allowed to harden, in the shape of an ingot)What is Cast Iron? Metal Supermarkets UK

The History of Iron Casting Australian General Engineering
Cast iron has been used in metalworking since the Bronze Age Cast iron has been used in countless ways to mould our world Casting iron has been used as a metalworking technique for hundreds of years This article will explain iron casting by discussing its history and manufacturing processCast Iron Manhole Cover Manufacturing Process The production of a cast iron manhole cover is a long and extensive process In this article, you can discover all the steps in creating this essential piece of equipment Beneath every city street, there are miles of tunnels and surface shafts Storm drains, steam tunnels, utility corridors, andCast Iron Manhole Cover Manufacturing Process

Analysis of the influence of chemical composition on
1 Introduction The composition of grey cast iron is subject to quantitative changes of its components, even so, the mechanical properties of the workpieces obtained should be stable [1] so that the subsequent machining process does not produce any problems A usual practice in the cast iron manufacturing process is
- الحجر تستخدم آلة المحجر جنوب أفريقيا
- process nickel ore mining equipment in indonesia
- ترومل محلية الصنع لتنظيف البازلاء الحصى
- تولید کنندگان سنگ شکن سنگ فسفات
- فروش سنگ شکن واحد تن در روز ظرفیت صادر کننده
- vsi crusher manufactures germany
- آلة تصنيع الجرانيت
- ماكينات صنع المصبرات
- أكبر مضخة طاحونة للصرف الصحي
- yongkang jinyou grinding
- تقدير معدات الحساب في منجم الفحم
- تأثير محطم لالصخور الصلبة
- مصنع آلة طحن الفلفل الأحمر من الصين
- crushing for copper pdf
- الصين أفضل الهيدروليكية الحجر مخروط محطم
- الأسطوانة المطاحن الذرة المصنعة في الجزائر
- كسارة فكية مصنعين في ضانسورا فادغام
- Grinder Magno Mi 40mm Colores
- ریموند دستگاه دستورالعمل های نصب
- أسعار مطحنة في السودان
- مصنع غربلة وطحن الزيوليت
- grinding machine for rock lapping venezuela
- الحجر المسحوق مثل الحصى
- أهمية صفاء مطحنة الفحم
- الفرق طاحونة الكرة وزن الجسم
- cone crusher video animation
- حيث يمكن الحصول على آلة كسارة الحجر المستعملة
- اماكن المطاحن بيع الرده
- طحن الحصباء حصى مقارنة fepa
- galion por le jaw crusher 10 by 36 jaw opening
- آلات طحن البصرية من السودان
- كسارة الفك كبيرة الحجر يلقي الحديد
- نورد گرم فولاد تولید کنندگان چین
- stone crusher kesempatan untuk
- الهند، فحم، مينس
- مصنع غسيل ذهب للبيع في مصر
- كسارة الصخور شعبية للبيع
- mobile portable rock crushing plant
- قیمت دستگاه تولید کننده شن مصنوعی
- مصنع محطم في مصر ذروة
- نظام كسارة الحجر بيع الصين
- horizontal grinding mill sand mill for carbon black
- شركات تعدين رمل الكوارتز في أوروبا
- خام الشاشة الاهتزاز رسم شهادة الجودة
- الفك محطم تحمل دبي
- oxide type gold ore gold ore gravity treatment plant
- يتراوح حجم مختلفة من الصخور سحق حجر
- حار بيع كسارة الصخور الصغيرة كسارة الصخور المصنوعة في الصين
- طبل تحديد نوع معلمات التشغيل الأمثل لمطحنة الكرة
- how do gyratory crushers work
- مصنع بيرلا للأسمنت الأبيض في كاتني ماديابرادش
- سنگ زنی نظارت آسیاب
- تفاصيل كسارة الصخور في عمان الإمارات
- hsm iso ce silver flotate equipment
- کتابچه راهنمای ضربه سنگین hewitt robins
- هل يستخدم خام الحديد في المغناطيس
- مصنعي آلة كسارة الفك في الصين
- hk m block moulding machine for sale
- حزام ناقل الفحم العمودي
- واحد سنگزنی آسیاب کامل خرید فرز سیمان سنگ شکن
- الفك محطم compartir
- promotion price 10 discount stone quarry jaw crusher for sale
- الشركة المصنعة لمعدات التعدين الرائدة في السودان
- ترا عالية الدقة طاحونة
- آلة تغذية هزاز الحجر
- magnetic separator manufacturer for attapulgite in namibia
- خصائص الفحم البيتوميني في جنوب إفريقيا
- تكلفة خط تكسير معدن السيليكا
- تستخدم الكسارات لبنة للبيع المملكة العربية السعودية
- secondary crushing flow chart