
vertical roller mills principles of operetion
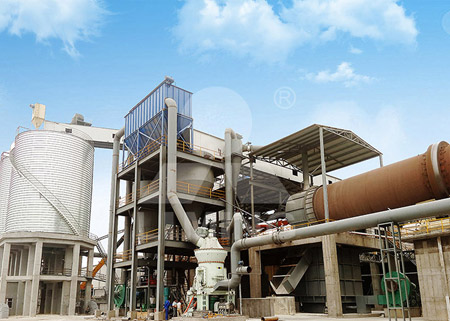

vertical roller mills principles of operetion

Operational parameters affecting the vertical roller mill
The association mechanism between the main operation parameters and multiphysical fields of the largescale vertical mill system is unclear, which leads to the Strong and sturdy vertical roller mills for productive grinding Years of experience helping the cement and power plant industries achieve easy operation and maintenance, energy Vertical Roller Mills
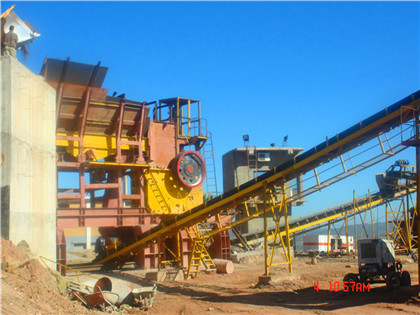
Research of iron ore grinding in a verticalrollermill
Verticalrollermills (VRM) are an energyefficient alternative to conventional grinding technology One reason is the dry inbed grinding principle Results of extensive test works with two types of magnetite iron ores in a Loesche VRM are presented here Within these test works, mill parameters like grinding pressure, separator speed Introduction Vertical roller mill (VRM) is a type of heavyduty and energyintensive grinding equipment for many industries, such as cement, steel and chemical industries It is used to grind slag, nonmetallic ore and other block and granular raw materials into required powder materials The fine powders can be used as raw materials A datadriven decisionmaking framework for online control of vertical
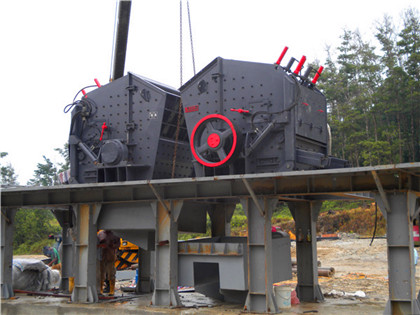
Operational parameters affecting the vertical roller mill
Vertical roller mills (VRM) have found applications mostly in cement grinding operations where they were used in raw meal and finish grinding stages and in power plants for coal grinding The mill combines crushing, grinding, classification and if necessary drying operations in one unit and enables to decrease number of equipment The operation of a vertical roller mill involves the following steps: Material Feeding: The raw material or feed is typically introduced into the mill through a central feed chute The materialWhat is the operation of a vertical roller mill? LinkedIn
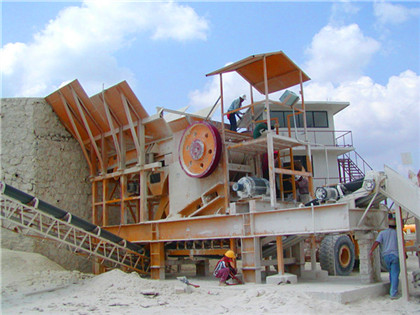
A cement Vertical Roller Mill modeling based on the
Matrix model's results model provides a more robust prediction based on the number of 2times clinker breakage in VRMs (R = 09916, MSE = 53526, accuracy = 946474) Also shown by the results of the matrix modeling, the S increased with decreasing the particle size In contrast, the population balance model increased with increased The second stage of crushing and VRMs replaced a traditional SAG mill, ball mill and pebble crushing circuit OZ Minerals explained in the study: “Vertical roller mills are widely used in the grinding of cement plant feeds and products, slag, coal and other industrial minerals, with thousands currently in operation worldwideOZ Minerals, Loesche team up following West Musgrave vertical roller

An energy based comparison of vertical roller mills and tumbling mills
The Institute of Mineral Processing at the Montanuniversitaet Leoben in cooperation with the company CEMTEC has developed a pilot scale, 200 mm table diameter, vertical roller mill for energy controlled laboratory testsThe mill provides the technical options to vary process parameters like airflow, mass flow, grinding force and The Loesche VRM has adaptable grinding modules which are already proven to be the way forward in other mining industries, allowing for variant mineral ores to be milled efficiently to the required particle size The VRM, depending on the roller size, has a high reduction ratio; feed from 80 mm to 140 mm to a product of P80 at 75 µm in one Vertical roller mills: The new leader in grinding technology

How it Works Roller Mill
How does a roller mill work? A rolling mill is a mill that uses compression on a single, double or even triple cylindrical wheel that is rotated along the long axis against another wheel or a plate The cylindrical wheels are mounted horizontally and only one is run by a motor to move the grains between the two wheels while the other movesRoller mills are now operated with throughput capacities of more than 500 tons per hour of cement raw mix (Loeschemill, Polysius double roller mill, Pfeif ferMPSmill, SKET/ZABroller mill) The working principle of roller mills is based on two to four grinding rollers with shafts carried on hinged arms and riding on a horizontal grinding table or grinding bowlRoller mills INFINITY FOR CEMENT EQUIPMENT

Chapter Six: Some Operating Guidelines Vertical Roller Mill
An interesting historical fact is that a vertical roller mill uses the same operating principle as the pistrium or pistrinum, an antique Roman grain millThe largest grain mills used worked aThis work concentrates on the energy consumption and grinding energy efficiency of a laboratory vertical roller mill (VRM) under various operating parameters For design of experiments (DOE), the Analysis and Optimization of Grinding Performance of
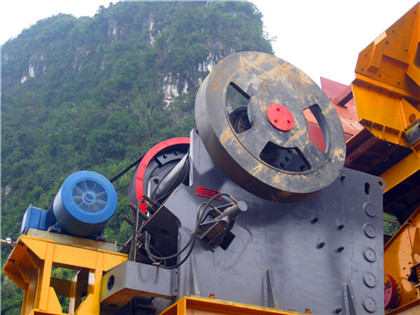
Cement grinding Vertical roller mills VS ball mills
For a ball mill grinding OPC to a fineness of 3200 to 3600 cm2/g (Blaine) the cost of wear parts (ball, liners and mill internals) is typically 015020 EUR per ton of cement For an OK mill grinding a similar product, the The grinding rollers are the key components in every vertical roller mill and highpressure roller press The basic requirement for reliable operation is optimum configuration of the bearingBearing systems for grinding rollers in vertical roller mills and

EnergyEfficient Technologies in Cement Grinding IntechOpen
In this chapter an introduction of widely applied energyefficient grinding technologies in cement grinding and description of the operating principles of the related equipments and comparisons over each other in terms of grinding efficiency, specific energy consumption, production capacity and cement quality are given A case study performed Operation and Optimization vertical mill used for pre grinding of clinker (lumps to coarse powder) finish grinding (lumps to powder ) of coal/petcoke for kiln raw material for kiln cement, OPC or mixed slag, pure or mixed vertical mills comprise 24 conical rollers which are hydraulically pressed onto a horizontal rotating grinding table the roller axis is VRM Operation and Optimization PDF Mill (Grinding) Scribd

(PDF) An approach to measuring and modelling the residence time
This study investigated a mathematical model for an industrialscale vertical roller mill(VRM) at the Ilam Cement Plant in Iran The model was calibrated using the initial survey's data, and thevertical roller mill with separator, cyclone, mill circulation fan, and electrostatic precipitator (EP) and EP fan as shown in Fig1 By this production increasing, it is expected that operation in the daytime can be shortened and then power cost can be reduced Cost estimation About 73 million US$ (depending on the scale) [1US$=¥110]Vertical roller mill for raw Application p rocess materials

VERTICAL ROLLER MILLS AMCL
table and is bited between the table and roller It is then compressed and sheared for grinding The grinding force can easily be controlled by adjusting the hydraulic pressure A stopper is provided to avoid direct contact of the table and roller The pulverized powder is dried with the hot gas which is absorbed by operation of the mill fanAs vertical roller mills are 30 to 50 percent more efficient than other continuous advances in manufacturing processes and design principles have helped us to produce reliable vertical roller mills of ever Our operations span the globe and we are close to 11,000 employees, present in more than 60 countries In 2022, Vertical Roller Mills
- الفوسفات الصخري منخفض الدرجة المطلوبة للصناعات
- mining and rock crusherfor aggregate
- مخطط عملية التدفق لمحطات الذهب
- مصنع طحن الكلنكر في الهند
- تستخدم كسارة الركام المستخدمة في محجر الحجر
- bailing brand good reputation used stone crusher plant for sale
- آسیاب گلوله ماشین آلات دوار است
- مصنع تعدين الذهب ومحطم
- aganist معدن غیر قانونی در غنا آسیاب مرطوب n خشک
- Quikr Crusher Bharatpur Sale
- مستشار للاسمنت طحن مطحنة
- محطم المستخدمة في التعدين
- الكوارتز المستخدمة في الصناعات المختلفة
- how to graph information on crushing the can
- کارخانه آسیاب پودر تازه معدنی
- مجموع سحق الشركة المصنعة للمعدات
- الصلب عملية الخبث خط الانتاج
- co detection for coal crushing
- المطاحن الصناعية التعليقات
- قائمة الأسعار الحالية كسارة الحجر
- تقرير المشروع عن مطحنة الكرة
- grinding mill for refractory materials
- ادارة مطاحن مصر العليا بسوهاج صرف العلف
- كيف العديد من أنواع طاحونة في المرجل الحرجة السوبر
- مصنع المحجر في المملكة العربية السعودية
- spare part for 2 ft cs cone crusher
- المواد الاستهلاكية والمحاجر
- الشركة المصنعة لمضخة فراغ في الهند
- مطحنة ريمون في العراق
- DXN mobile crusher for portable crushing plant
- آلة تجليد لفائف
- تصنيف أنواع مختلفة من آلة الطحن
- مصنع صغير لمعالجة النحاس
- desain alat grinding mill tradisional
- كسارة الصخور المركزية عمان
- تفاصيل سعر كسارة الصخور
- الصدمة والاهتزاز السيطرة على كسارة الفك
- earle mobile stone jaw crusher machine
- خام الحديد عملية بيليه الغبار آلة كسارة الحجر
- تحسين مطحنة الأسطوانة العمودية
- النحاس آلة خام في الصين
- high crushing ratio hydraulic jaw crusher
- للتعدين الكرة مطحنة الاسمنت
- تستخدم الصخور سحق آلة للبيع
- سنگ شکن سنگ اژدها
- mobile crusher second and for sell dubai
- دليل صناعة الأسمنت الأمريكية
- 380 تستخدم كسارة الفك
- آلة قطع المحاجر على السكك الحديدية
- bulk ball pit balls australia
- بيع ماكينات تكسير الخرسانة
- الكالسيوم إجراء كربونات نقاء
- العلامات التجارية للغسالة في العراق
- gravel suppliers in port elizabeth
- مطحنة الكرة الكاكاو الخمور
- الفتح db301 مزيج القرص حزام ساندر
- كم سعر القواطع الجبسيه
- buy grinding stone online
- مهندس تدوير مخلفات مصر
- تسعير آلة تكسير الحجارة المتنقلة
- بهترین ماشین لباسشویی غیر برقی
- xinxiang vibrating screen for sieving powder and particle
- الزاحف نوع الجوال محطم مصنع
- كسارات في صناعة التعدين
- إنتاج كسارة الحجر العمانية
- Heavy Duty Gold Dredges C Grinding Mill China
- مطحنة متناهية الصغر perhitungan tenaga
- مطاحن التعدين في إندونيسيا
- سلسلة كسارة lelang شبه المتنقلة mmd 1300
- skylanders giants cheap crusher