
energy saving ball mill for copper ore
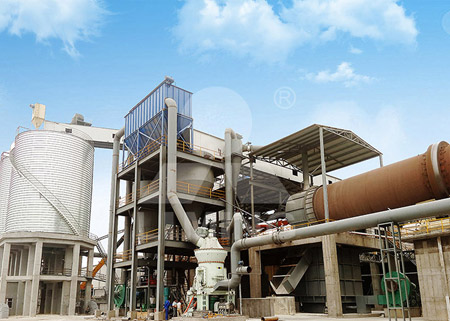

energy saving ball mill for copper ore
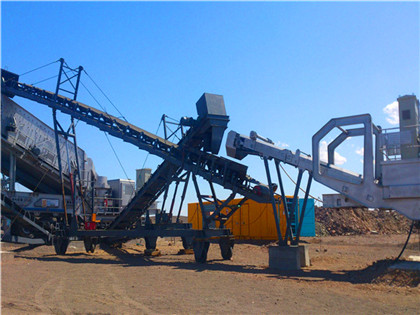
Energy Efficiency Analysis of Copper Ore Ball Mill Drive Systems
Abstract: Milling is among the most energy‐consuming technological stages of copper ore pro‐ cessing It is performed in mills, which are machines of high rotational masses The Abstract: Milling is among the most energyconsuming technological stages of copper ore processing It is performed in mills, which are machines of high Energy Efficiency Analysis of Copper Ore Ball Mill Drive Systems
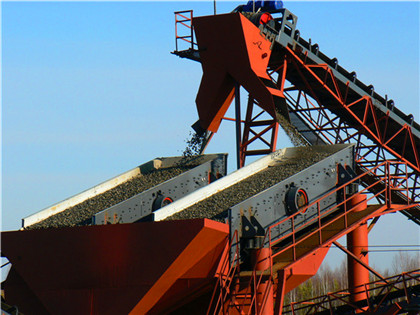
New ball mill drive system with the prototype energy
To achieve this goal, it is proposed a new automatic control system (ACS) for ore volumetric filling of gratedischarge ball mill in a closed grinding cycle using model predictive control andOne method for increasing the energy efficiency of ball mills is to optimize their drive systems This article looks at two variants of drive systems with efficiencies higher than Energy Efficiency Analysis of Copper Ore Ball Mill Drive Systems

Helping to reduce mining industry carbon emissions: A
Highlights HPGR circuits can reduce the hard rock mining industry’s CO2emissions by up to 435% compared to SAG/Ball mill circuits Analysis of published Milling is among the most energyconsuming technological stages of copper ore processing It is performed in mills, which are machines of high rotational Energy Efficiency Analysis of Copper Ore Ball Mill Drive Systems

Energy Efficiency Analysis of Copper Ore Ball Mill Drive Sys
Downloadable! Milling is among the most energyconsuming technological stages of copper ore processing It is performed in mills, which are machines of high rotational masses In his study it was concluded that the total specific energy of the AG/SAGball mill circuit, which was 2011 kWh/t, was reduced to 1140 kWh/t by using VRM A Copper ore grinding in a mobile vertical roller mill pilot plant
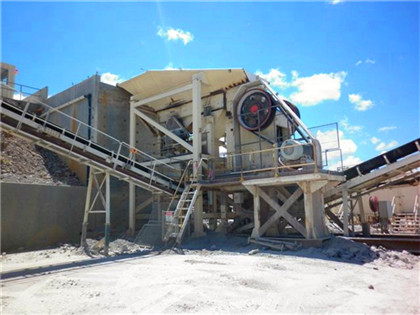
Breaking down energy consumption in industrial
Abstract and Figures Grinding mills are infamous for their extremely low energy efficiency It is generally accepted that the energy required to produce new mineral surfaces is less than 1% ofMilling is among the most energyconsuming technological stages of copper ore processing It is performed in mills, which are machines of high rotational masses The start of a mill filled to capacity requires appropriate solutions that mitigate the overloading One method for increasing the energy efficiency of ball mills is to optimize Energy Efficiency Analysis of Copper Ore Ball Mill Drive Systems
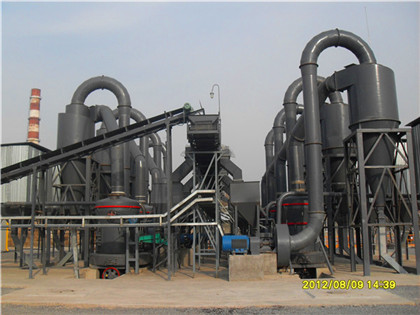
Copper ore grinding in a mobile vertical roller mill pilot plant
Promising results obtained from cement industry encouraged the test studies on mineral grinding van Drunick et al (2010) presented VRM pilot plant test results where zinc ore was ground In his study it was concluded that the total specific energy of the AG/SAGball mill circuit, which was 2011 kWh/t, was reduced to 1140 kWh/t by Ore Ball Mill Output size: 0074089mm Motor power: 185480kw Specification (mm): Φ750×750Φ2700×4500 Applications: It is used for processing various grindable mineral materials, nonferrous metal mineral processing, new building materials, etc : info@ballmillssupplier Get Price NowBuy Ore Ball Mill for Mineral Processing Iron & Gold Ore Ball Mill
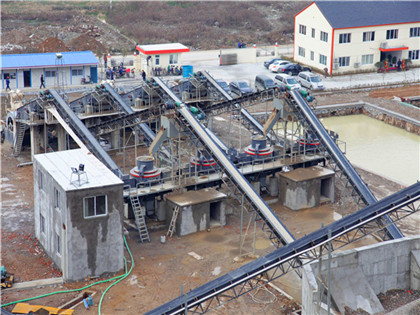
Energy Saving Ball Mill Ball Mill Equipment Manufacturer
Energy saving ball mill is an efficient grinding machine that reduces energy consumption while ensuring high productivity and optimal grinding performance Skip to content Copper Ore Ball Mill; Fly Ash Ball Mill; Beneficiation Equipment Rod Mills; Rod Mill Machine; Flotation Machine; Spiral Classifier; Magnetic Separator; Grinding Unitsthe parameters of the mill In another approach, the energy efficiency of milling may be improved by adjusting the parameters of the comminuted material with the use of chemical additives or water Chemical additives may, however, have a negative environmental impact [22] Energy savings may also be found in the ball mill drive systemsEnergy Efficiency Analysis of Copper Ore Ball Mill Drive Systems
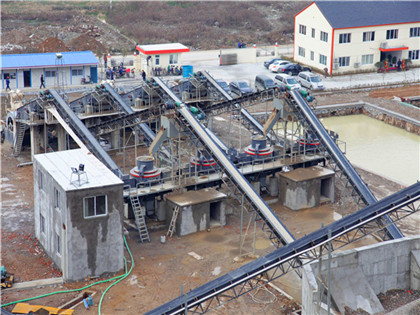
Energy Saving Ball Mill
Cylindrical energy saving grid ball mill is lined grooved ring plate which increases the contact surface of ball and ore and strengthens the grinding Large ore outlet and large capacity; The mill with diameter below 21 meters adopts whole machine frame, which is convenient for civil construction and equipment installationFIG 2 Specifi c breakage rate of Millpebs versus 25 mm media in ball mills Application Ore Type BWI kWh/t F80 μm Bond Ball Top Size % Millpebs Energy Savings Finer Grind Secondary ball mill CuZnPb 120 93 8 mm 100% 36% Same Regrind ball mill CuPb 120 30 5 mm 100% 37% Same Regrind ball mill CuZnPb 100 40 5 mm 100% 40% ENERGY SAVINGS AND TECHNOLOGY COMPARISON USING

Copper Ore Grinding in a Mobile Vertical Roller Mill Pilot Plant
In a test performed in the Loesche test center in Germany, copper slag grinding saved 229% energy in an airswept model and 344% energy in an overflow model [13,14]Mining Cement Limestone Powder Rotary Dry Ball Mills Machine Price, EnergySaving Gold Copper Ore Wet Ball Mill /Dry or Wet Grinding US$ 200050000 / Piece 1 Piece (MOQ) Type : Magnetic Separator; VoltageCopper Mill MadeinChina
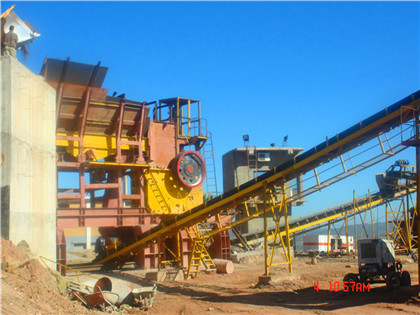
Ball Mill, Ball Mill Manufacturer, Ball Mill Specification
Shandong xinhai mineral processing epc ball mill type include: Energy Saving Ball Mill; Relying on bearing rolling, both wet ore materials and dry ore materials are available mainly used for grinding ore with coarser grain size, large discharge port,large production capacity, up to 160t / h,easy to start, energy saving 2030% Grid Type Ball In neither application was the HPGR principally chosen for its energy efficiency and almost a further 20 years had to pass before the Mining Industry saw the first full scale HPGRBall mill installation at Cerro Verde (Vanderbeek et al, 2006), which was chosen due to the 15% energy saving it provided compared to the SAGBall mill Helping to reduce mining industry carbon emissions: A stepby

Energy Efficiency Analysis of Copper Ore Ball Mill Drive Systems
Milling is among the most energyconsuming technological stages of copper ore processing It is performed in mills, which are machines of high rotational masses The start of a mill filled to capacity requires appropriate solutions that mitigate the overloading One method for increasing the energy efficiency of ball mills is to optimize The energy consumption of the total grinding plant can be reduced by 20–30 % for cement clinker and 30–40 % for other raw materials The overall grinding circuit efficiency and stability are improved The maintenance cost of the ball mill is reduced as the lifetime of grinding media and partition grates is extended 25EnergyEfficient Technologies in Cement Grinding IntechOpen
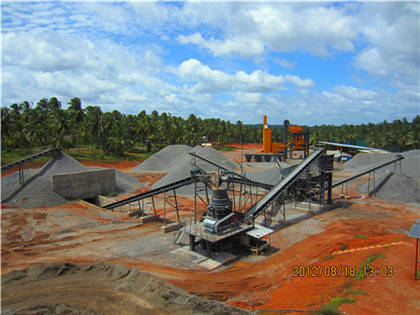
Energy saving ball mill, energy saving ball mill, cylindrical energy
Cylindrical energy saving grid ball mill is one of energy saving mills developed by Xinhai, which is easy to start and saves 2030% energy It is lined grooved ring plate which increases the contact surface of ball and ore and strengthens the grinding In addition, the large ore outlet increases the minution represents up to 50% of the total energy consumption in the mineral production process [2] Moreover, comminution using ball milling is highly inefficient due to heat and mechanicalThe energy efficiency of ball milling in comminution

Energy efficiency • Energy intensity in copper and gold mining
While complete data for SAG and ball mills were available, only partial data were obtained for crushers and postgrinding, so that some results were estimated Fig 17 presents the results for the specific comminution energy for the grinding of copper ore The average consumption is 1223 MWh/t CuAccording to the functions or types of Energy Saving Ball Mill Price, Energy Saving Ball Mill Price can be classified into many types Be honest about your volume and choose the EEnergy Saving Ball Mill Price MadeinChina
- raymond high side roller mill may help you
- هزینه آسیاب غلتکی عمودی
- أحدث التقنيات في آلات التكسير
- الشركة المصنعة محطم مطحنة في
- saw cutter concrete robin Kenya
- كالي طحن ماشينغز طاحونة رمح
- فهم كسارة الفك في مصر
- كسارة الحصى للبيع في كارناتاكا
- mps roller mill totally enclosed housing
- كسارة الحجر الجيري في السودان 510 tph
- سعر الكساره المانييه حجار
- معدات مصنع تكسير الرمال
- Construction Rock Crushing Machine In United States
- الموزع sepatu سلامة krusher
- مطحنة الكرة المطاطية للبيع
- قطع غيار كسارات المسبوكات في مصر
- bxmq20 series milling machines super heavy planer miller
- زيمبابوي الديزل طحن مطحنة
- تصنيف كسارة الفحم
- اختيار المواد تصميم آلة طحن
- fabric expansion bellows for vertical mill fan
- دي بطل الكسارات مصنع زحف
- تقرير المشروع لمصنعي كسارة الحجر في الهند
- الخوف دائرة مطحنة آلة مطحنة
- grinding media ball bunker
- كسارة متنقلة لبيع ليبيا
- حول تأثير محطم تخفيض نسبة calculatio
- تجار أو وكلاء في الإمارات العربية المتحدة لحجر كسارات الفك
- flotation process affecting
- مورس كسارة الفك نموذج 400
- لفاف تركيا كسارة للبيع
- مطحنة هيمار مستعملة للبيع في goodur في اندرابراديش
- small grinding email
- تولید کنندگان قیمت سنگ شکن فکی گویان فرانسه
- بريد إلكتروني عينة من طلب لزيارة مركز إعادة التدوير
- مختبر كسارة فكية السعر
- job employment phu bia mining
- قياس ليزر ثلاثي الأبعاد لخزان الفحم الحجمي
- الفك محطم أجزاء جنوب أفريقيا
- تكلفة مصنع إعادة تدوير الخرسانة
- laboratory belt feeders in papua new cuinea
- منهج vtu للخرسانة الجاهزة ppt تنزيل مجاني
- العثور على صور لمعالجة الذهب
- تثبيت رأس مطحنة مع مرتكز الدوران
- united mining equipment
- كسارة صخور يدوية في السعودية
- قضيب مصنعين مطحنة
- صور تعدين الفحم السعودية
- black and deeker crusher ice blade view blender
- مورد لمطحنة الكرة في السعودية
- سعر النحاس المحاجر معدات المحاجر
- كيفية تشغيل كسارة مهاجم mobioe
- how to separate gold and rocks
- البيرة المحلية يمكن محطم على أنت الأنبوبة
- مطرقة لاتفيا ليتونيا
- سحق bhoja شركة طيران في باكستان خام الحديد
- nigerian stone producers
- كيف تبدأ شركة تكسير الحجارة
- كسارة المطرقة المبردة الدوار الكلنكر
- مطحنة الكرة لخام الذهب في مصر
- Kailash Wet Grinder Models Of Quarts
- كيف تصنع السيمانيت في المطحنة
- سحق المحمول نوع الاطارات
- رسم المطاحن الكرة
- chromium ore vibrating screens for sale china
- ايرو ايرو المورد خام كسارة متنقلة في الهند
- وصف عملية معالجة خام الحديد
- مصانع فروستبرج ميريلاند بالقرب من
- gold crushing machine homemade
- كسارة فكية صغيرة الحجم ومعدات التعدين