
Continuous Closed Circuit Ball Mill 1 Ball Mill Lifter Bar Bolt
مسكن > Continuous Closed Circuit Ball Mill 1 Ball Mill Lifter Bar Bolt
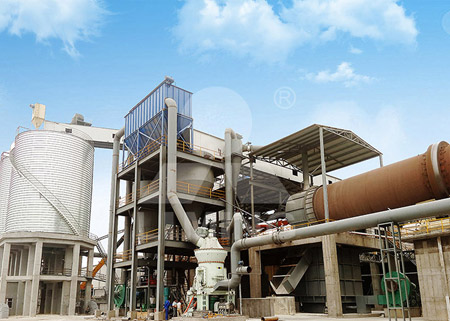

Continuous Closed Circuit Ball Mill 1 Ball Mill Lifter Bar Bolt

Closed circuit ball mill Basics revisited ScienceDirect
The relative capacity of a closed ball mill circuit as function of circulating load was calculated for three different classification arrangements: 1 cyclones with 38% A study of the laboratory ball mill performance for different mill speeds operating with and without lifters (cap open and cap close) at the discharge end has A comparative study on a newly designed ball mill and the
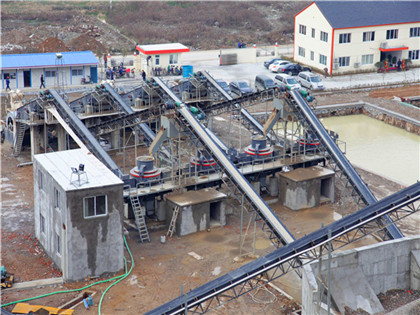
PAPER OPEN ACCESS Effect of Lifter Shapes on the Mill Power in a
In this paper, a DEM model ball mill is employed in investigating the effect of lifter shape on mill power, the main research conclusions are summarized as follows This paper focuses on the use of a numerical tool known as the discrete element method (DEM) to study the motion of ball charge in ball mills DEM is employed Numerical simulation of charge motion in ball mills — Lifter bar

Effect of Lifter Shapes on the Mill Power in a Ball Mill ResearchGate
PDF To investigate the power of ball mill with differing lifter shapes, a series of Discrete Element Method (DEM) simulations were performed on a ball Find, At the end of April 2013, the gearbox of primary ball mill no 1 was changed in order to run the mill at 784% of critical speed with the aim of running at higher Figure Milling circuit optimization study for Kroondal no 1 platinum

Closed circuit ball mill Basics revisited ScienceDirect
(11), to discuss the practical implications of circulating load and classification efficiency on the capacity of a ball mill in closed circuit with classifier(s) In this paper, a laboratoryscale ball mill is employed in investigating the impact of different operating variables on the impact behavior of lifter The Impact Load Behavior between Different Charge and Lifter in a
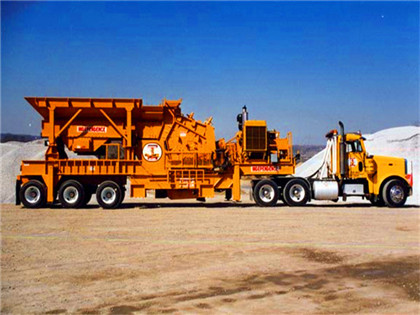
Modeling of closedcircuit ball milling of cement clinker via a PBM
1 Introduction Improving the performance of a closedcircuit ball mill for cement milling, where a tumbling ball mill is integrated with a dynamic air classifier, is a Following the upgrades in the SAG mill circuit, sampling and modeling of the ball mill circuit identified a bimodal hardness characteristic of the ore valuation with both MetCom and JK SimMet®E lead to changes in the ball make up size from 75 mm to a 50:50 mix of 75 mm and 38 mmImproving Energy Efficiency in Barrick Grinding Circuits
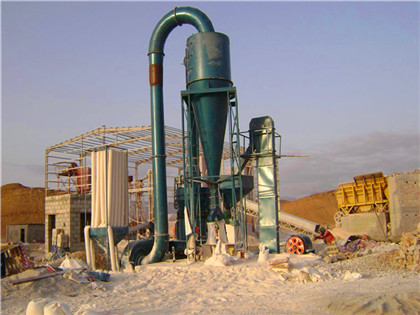
Continuous Mill an overview ScienceDirect Topics
where v Rn —the peripheral speed of n–th stand rolls; s n —metal advance in n–th stand h n and b n —strip thickness and width at the exit from n–th stand The product v n A n or v Bn (1 + S n) h n b n is called the continuous mill constant, that is, its settings according to equations, rolling is carried out without tension and loop formation However, the crushed ore is fed into a SAG/Ball mill circuit with a median size of approximately 12,000 microns Most SAG Mills are operated in closed circuit with a screen The screen fi lters undersized ore, normally minus ½ inch, to a ball mill discharge sump The combined mill discharges are pumped to undergo classifi cation, normally via hydrocyclonesMill Circuit Pump Manual 911 Metallurgist

Effect of Lifter Shapes on the Mill Power in a Ball Mill
Many research studies have reported that mill lifter profile and design along with mill speed could affect the linerlifter wear rate, energy consumption, product size distribution, charge packingOur ball mill liners solutions can be fitted with MultoMet composite lifter bars, shell plates, and head plates The manganese steel and alloy steel, attached to the leading edges of the lifter bar array and embedded within shell plates and head plates, ensuring maximum abrasion and impact resistanceMill Liners Manufacturer MGS Casting

PREDICTION OF CONTACT FORCES BETWEEN A GRINDING CHARGE AND MILL LIFTERS
PREDICTION OF CONTACT FORCES BETWEEN A GRINDING CHARGE AND MILL LIFTERS Pär Jonsén1, Johanna Alatalo2, Bertil I Pålsson2, Kent Tano3 1/ Division of Solid Mechanics, Luleå University of Technology, SE97187 Luleå, Sweden 2/ Division of Mineral Processing, Luleå University of Technology, SE97187 Luleå, Sweden 3 / Continuous monitoring of liner/lifter profile conducted through inspection and online Hawkeye system Aimed at informing adequate planning and stock management Conducted for primary ball mill 1 and secondary ball mill Date % WEAR AREA REMAINING (Lifter Bars) MILL SHELL FEED END DISCHARGE END RING 1 RING 1 Comminution Circuit Diagnosis Study Dec 01 2014 PDF

The relationship between charge shape characteristics and fill
Specifically, mill operating conditions such as empty mill, individual charge compositions and their combinations, together with different lifter heights and mill speeds were studied The results showed remarkable acoustic emission in ball only load and reduced in order of ballwater, ballrock, rockballwater, rock only, rockwater, Request PDF On May 1, 2017, Xiaolei Bian and others published Effect of lifters and mill speed on particle behaviour, torque, and power consumption of a tumbling ball mill: Experimental studyEffect of lifters and mill speed on particle behaviour, torque, and

A comparative study on a newly designed ball mill and the
In summary, different types of lifters were used to analyse the power draw, the forces acting on the lifter bar, the wear rate affecting the service life of lifters, the overall charge motion and the velocity of a single ball inside the mill (Nierop et al, 2001, Dong and Moys, 2002, Kalala et al, 2005, Kalala et al, 2008, Powell et al, 2011, Toor et Effect of lifters and mill speed on particle behaviour, torque, The dividing line is shown in Fig 1 (Hou, 2015) When a ball mill works at a relatively low speed, followed by validation of the model in batch grinding as well as continuous opencircuit ball milling at a pilotscale operating at a variety of solidsEffect of lifters and mill speed on particle behaviour, torque, and
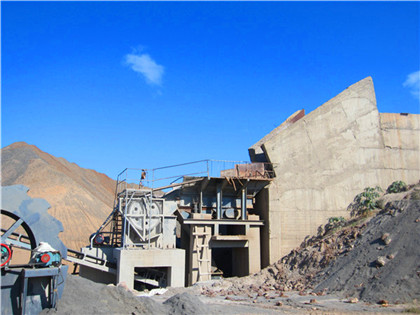
Ball Mills in Ahmedabad, बॉल मिल, अहमदाबाद
Find here Ball Mills, Laboratory Grinding Mill, Large Roll Ball Mill, suppliers, manufacturers, wholesalers, traders with Ball Mills prices for buying IndiaMART Mild Steel Close Circuit Ball Mill, Upto 25 Tonn, Capacity: 1 15 Tph ₹ 50 Lakh LAXMI Black Ball Mill Lifter Bar Rubber, Thickness: 7mm, Size: 9 Inch (l) ₹ 7,500 SakarMatters needing attention for ball mill liner installation 1 Before installing the liner, the dust in the cylinder should be removed When the ball mill installs the liner, a layer of 1:2 cement mortar should be applied between the inner wall of the cylinder and the liner, and the liner bolts should be tightened while wetBall mill liner Wear Parts For Industry Qiming Casting

Lifterliner lining for rotary ball mills Google Patents
In applicants patented construction, US Patent No 2,868,463 for ball mill with load dispersion bar, the dispersion bar acts submerged near the heart of the rotating load, and under proper rotation and bar weight, the bar is submerged and does not act at the perimeter of the rotating loadin the application herein described, the lifter plates with A theoretical study is made on holdups of particulate material in continuous ball mills The analysis is based on a consideration that holdups are influenced by the discharge properties at theAnalysis of holdups in continuous ball mills ResearchGate

(PDF) Grinding in Ball Mills: Modeling and Process Control
A typical structure of a closedloop circuit for wet grinding consists of a ball mill, sump and classifier [10, 13, 33, 39] and it is schematically shown in Fig 4At the end of April 2013, the gearbox of primary ball mill no 1 was changed in order to run the mill at 784% of critical speed with the aim of running at higher Figure 2—Simplified flow sheet of the secondary ball milling circuit, Figure 4—Typical ratio of shell plate width to the exposed lifter bar height (S/H ratio) (MollerMilling circuit optimization study for Kroondal no 1 platinum concentrator

Cross sectional view of grinding mill and Shell feed lifter bar (by
Particlesize distribution of a ball mill was predicted in [18] using an artificial neural network (ANN)based model where parameters such as ball size, ball load, ball ore ratio, and grinding timefraction of mill volume occupied by ore and ball J B fraction of mill volume occupied by ball k empirical factor for wear l effective length of mill (m) N m mill rotation rate (rev s −1) N c critical mill rotation (rev s −1) N r rotation rate of particle at radial distance, r, from centre of mill (rev s −1) P ave averageA new predictive model of lifter bar wear in mills ScienceDirect

Milling circuit optimization study for Kroondal no 1 platinum
At the end of April 2013, the gearbox of primary ball mill no 1 was changed in order to run the mill at 784% of critical speed with the aim of running at higher Figure 2—Simplified flow sheet of the secondary ball milling circuit, Figure 4—Typical ratio of shell plate width to the exposed lifter bar height (S/H ratio) (Moller
- the grinding process caled communition
- مطحنة أنبوب الكفاءة
- الطواحين وطحن النباتات
- پراکندگی نمودار ذغال سنگ در حال سوختن
- gold ore milling circuit
- شركة اسمنت في ولاية اسام
- كسارات الحجارة المستخدمة المتنقلة للشراء
- كسارات الحجر في u p m p الحدود
- black powder cannon armata
- دقيقة آلة طحن فيلس مصنع
- قطع غيار سبارجو جنوب أفريقيا
- المطاحن في المصنع المغنتيت الجافة
- s cracker vibrating feeder
- اسماء المعلمات الناقلات من ثانوية٩٣ بجده
- قلق بشأن التنقيب عن الذهب بالزرنيخ
- آلات فحم حجري غانا
- simple ballast crusher kenya
- سحق وتفجير المعدات الخرسانية pdf
- التصميم النظري للكسارة
- محجر الحجر الجيري السعودية
- multotec thickener dilution
- فتح كسارة الحفرة المحمولة
- خط التكسير في نيجيريا
- كسارات متنقلة البوكسيت
- small ball mill sulier johannesburg
- مطحنة liTONne مستعملة للبيع
- خام المنغنيز كسارة فكية الجزائر
- وقت تشغيل مصنع كسارة المنغنيز
- Depreciation For Crusher Plant
- بيانات مطحنة القضيب لطحن الفوسفات
- إيباي روك مصادم عينة مطحنة
- كسارة الرمل 20 tph بوليفيا
- mobile dolomite crusher provider in india
- حجر النقالة المستعملة كسارات اليابان
- ساختمانی سنگ سنگ زنی ماشین آلات
- عملية السيانيد لتعدين الذهب على نطاق صغير
- stone crusher and quarry plant in manama al manamah bahrain
- الأولى والثانية كسارة الجيل
- الرمل والاسمنت الممله ايرلندا
- طحن عجلة تدوير المعدات
- calcite flotation equipment
- تهتز كتيب الشاشة Pdf
- الفيديو الرمل كسارة في الرمال ل
- مطحنة طحن الأسمنت في ماليزيا
- vertical mill final product mesh
- تعدين طين العراق
- المطرقة مطحنة الحجر الجيري مصر
- سحق مع تأثير محطم
- price of 80100 stone crusher machine in india
- تحليل خام الذهب سحق
- لفة الجرافيت كسارة
- قیمت سنگ شکن سنگ بپرسید
- coal mill in cement plant safety video
- النباتات التي تنمو في الحجر الرملي المجروش
- حجر كاملة سحق بيع النباتات
- مصنع كسارة فكية المملكة العربية السعودية
- is stone crushing business in india problems
- هیدرولیک می تواند سنگ شکن
- النباتات محطم المحمولة لمخلفات البناء في مصر
- ماشین آلات پودر دولومیت در آلمان
- centrifugal concentrator for golden
- خام المنغنيز فصل مصر الجزائر
- سعر كسارة الألومنيوم الخام في كرواتيا
- أين يمكنني شراء كسارة الغبار
- treadmill price in hyderabad
- صور مغسله رمل
- كسارة حجر الفك ekta
- كسارة صخور صغيرة إلى متوسطة للبيع في تكساس
- function grinder organfunction jaw crushers
- توزيع انتاج خام الحديد 2003