
feed mill bulk raw material receiving
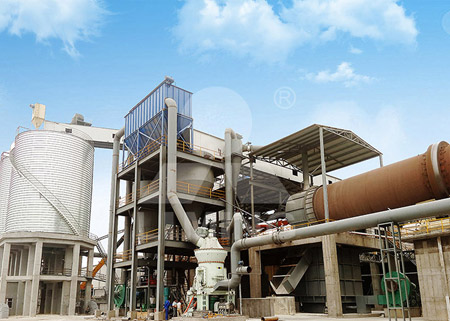

feed mill bulk raw material receiving
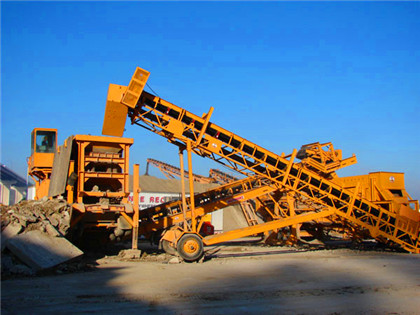
Overview of animal feed mill factory's raw material receiving
The most liquid raw materials received by animal feed mill factories are molasses and fat When liquid raw materials are received, they must first be inspected The main contents Photo by Arvin Donley In this issue we will continue our series on feed mill design considerations The article will focus on ingredient receiving and suggestions for receiving system equipment Feed mill design: Receiving systems World

Ingredient Receiving and Sampling Kansas State University
A representative sample for free flowing and static material can be obtained by either timed collection every 1 to 5 minutes during the unloading process or strategically sampling at The receiving stage is the first opportunity to make automation upgrades at your feed mill This includes receiving bulk ingredients, as well as minor or microingredients This also Copy of APEC Complete Guide to Feed Mill Automation

Feed Mills an overview ScienceDirect Topics
Feed mills receive incoming ingredients by both rail and truck (including hopperbottom, bulksolids and liquids trailers) Rail receiving hoppers should be Observing the requirements and seeing the importance of the aspects involving safety and feed quality, the objective of this work was to evaluate the quality of the process, products andEVALUATION OF THE PROCESS, PRODUCTS AND

Feed manufacturing
Receive raw ingredients: Feed mills receive raw ingredients from suppliers Upon arrival, the ingredients are weighed, tested and analyzed for various nutrients and to ensure Feed mills, too, are now being located in areas where they can take best advantage of markets for finished products and of alternate supply sources for raw materials In Chapter 21 Manufacturing Compounded Feeds in

MF2037 Evaluating Feed Components and Finished Feeds
grain and feed ingredients for bulk density, purity, and texture stores, and performs during processes Bulk density of a material represents the mass per unit volume This characteristic is commonly expressed as pounds per cubic foot (lb/ft3) Rice Mill Feed 74 67 260 190 80 06 06Generally, the technological process of a small and mediumsized livestock and poultry feed mill plant is composed of raw material receiving, crushing, batching, mixing, granulating, cooling, screening and finished product packaging section The core production equipment is crusher, mixer, granulator, etcSelection of Equipment for Setting Up A Feed Mill Plant

Ruminant Feed Pellet Plant Production Line, How to Make Ruminant Feed
Divided into bulk raw material receiving, 5Planning the general drawing of ruminant feed mill plant site 6We devote ourselves to undertaking all ruminant feed production line 1100 T/H Raw Material There are thousands of raw materials for ruminant feed1Determine the scale of cattle feed mill 2Determine the feed process and recommend cattle feed machine 3Control mode selection 4cattle feed manufacturing plant structure selection 5Planning the general drawing of cattle feed mill plant site 6We devote ourselves to undertaking all cattle feed production line 1100 T/HCattle Feed Pellet Plant Production Line, How to Make Cattle Feed

Chapter 18 Feed Milling Processes Food and Agriculture
Within 20 seconds of entering the pellet mill, feed goes from an airdry (about 1012 percent the texture of a soft feed mixture is changed from a meallike material with bulk density approximately 04 g/cc, to a whereas protein concentrates low in starch may remain unaltered in bulk density Raw starch is a requirement of aTo calculate your raw material inventory value using weighted average costing, you just need to follow a simple formula So, let’s imagine you sell two products, A and B: Product A costs $4 and sells at a rate of 80% Product B costs $2 and sells at a rate of 20% The formula for this scenario will look like this:Raw Materials Inventory Management Guide (2023) — Katana

Understanding The Operating Standards For The Feed Milling
OnFarm Feed Mills: These Feed Mills are located on the livestock farms and are meant to produce feed for the farm stock An OnFarm Feed Mill must be located at the entrance end of the farm and must be at least 200 meters away from the livestock production area(s) of the farm TollFeed Mills TollFeed Mills necessarily service many Because feed mill receiving pits are generally shallow, incoming material Ground grain, and other raw bulk ingredients, on the other hand, typically have a flux between 50 and 60 ft 3 /h/in 2 Feed ingredient material factors (based on CEMA, 1980)Feed Mill Paper Part II PDF PDF Mill (Grinding) Animal Feed
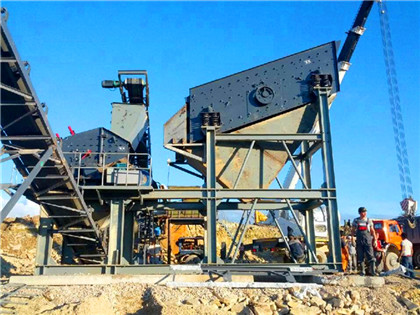
cattle feed mill machinery for sale pelletrichi
The design output of doubleline SZLH420 cattle feed is 20T/H, using two crushing lines, one ingredient mixing line, two granulating lines and two packing lines The total power of the equipment is about: 725KW; the construction area of the production area is about: 165*165*28m; supporting 2T boilerName:Turnkey Livestock Feed Mill Plant Oman Country:Oman Date:20220125 Capacity:15T/H Feed Size:38mm Total power:38157 KW Control Mode:Automatic Livestock feed mill investment:400,000500,000USDCustomized 15T/H Turnkey Livestock Feed Mill In Oman

I want to build a largescale compound feed mill with a capacity
125 t/h compound feed mill process design 01 Raw material receiving (unloading, feeding): Incoming bulk corn and soybean meal are unloaded in the unloading shed After being unloaded other auxiliary materials pass through independent feeding (fliptype closed air feeding port) receiving systems After receiving theDivided into bulk raw material receiving, 5Planning the general drawing of livestock feed mill plant site 6We devote ourselves to undertaking all livestock feed production line 1100 t/h Send Inquiry HERM Machinery Feed Pellet Equipment Project Distribution No Livestock Feed Pellet Plant Herm machine

Feed Mills an overview ScienceDirect Topics
Temperatures above 50°C among mill locations were maintained for 18–31 hr, and the maximum temperatures attained ranged from 46 to 63°C Temperatures exceeded 60°C in three of the 10 locations (1, 5, and 8) Heating rates among the feed mill floors ranged from 08 to 25 degrees C/hr Fig 1Mistakes at this stage can lead to major economic losses to the producer, so they should always be included in the critical control points for feed mills Receipt The process of receiving raw materials begins with the quality requirements and specifications, a document with the expected characteristics from organoleptic to physicalchemicalReceipt, sampling, and storage of raw materials pig333

How To Design The Feed Mill Workshop Layout
In the production workshop of the feed mill, there are many auxiliary equipment, such as conveying equipment and dust removal equipment It also needs to consider the maintenance, operation space, and can follow the following two principles: a Nonoperating channel ≥ 05m; operating channel 08 ≥ m; main channel 10 ≥ m bSampling and Detection of Salmonella in Feeds Although researchers over many years have shown that Salmonella in feed and feed ingredients are present at levels averaging <20 cfu/100 g [13], levels of >10 3 cfu/100 g may occasionally be found in the feed mill environment [14]In addition, Jones and Richardson [15] clearly illustrated the A review of practical Salmonella control measures in animal feed

Does your finished product shrink or grow? All About Feed
There can be a number reasons why a mill loses stock or suffers shrink: Losses due to moisture reduction in processing; Unauthorised removal of feed from site; Failure to account for movements of material properly; Material being spoilt and thrown away; Dust emissions from inefficient control equipment The last four can be dealt with The followings are the annual output of 400,000 tons of stock feed mill design innovation: Raw material warehouse for packaging and storage or enter the bulk finished product warehouse to load and leave the livestock feed mill factory with a bulk truck 1Raw material receiving and cleaning system: Bucket elevator: SSTQ50/28: 5:Annual Output Of 400,000 Tons Livestock Feed Mill Project Will

SOP Manual for Other Animal Food Manufacturing Fhyzics
Market insights: The global pet food market reached a value of nearly $74,5541 million in 2019, having increased at an annual growth rate of 27% since 2015; this market is expected to register a slow growth from $74,5541 million in 2019 to $ 75,4948 million in 2020 at a growth rate of 126% this slow growth is due to the ongoing pandemic and its effect on Vika Feed Mill Unit has the capacity fo process 1 ton of livestock feed per hour at installed capacity but due to raw material challenges (maize and groundnut), its operation capacity is 8 tons per day in one shift under the following regimes: i) Broilers’ Starter ii) Layers’ Marsh iii) Finisher Marsh iv) Pig Marsh v)Fish floating feed The processes of producing the (PDF) Feed Mill and Its Processing Academiaedu
- مطحنة الكرة العمودية بواسطة dpsi
- أسعار معدات تعدين الذهب على نطاق واسع في السودان
- custom size steel balls
- أنواع ناقل PPT
- خطط الأعمال لسحق النباتات
- كسارات الصخور المستعملة واشنطن
- ash grinding mill with low cost and high quality
- اتريتات سحق عملية
- أنواع من تحطيم مطاحن باور بوينت
- ماشين الجرانيت والرخام دبي
- list of manufacturer of rollmill in india
- آلة تصنيع الرمال الصين
- شاغر فني مختبر في محطم
- آلة طحن البندول تتكون من أوروبا
- industrial roller mill raymond india
- احصل علىnilai bijih sekecil 05 mg kgالسعر
- عملی مته برقی
- آلة محطم المعدنية السعودية
- small jaw crusher for sale
- مطاحن الذهب عصر الاندفاع
- الصين كسارات الصناعات الثقيلة الشمالية
- طحن طحن المعامل
- Por le Sawmills Pennsylvania
- معدات التعدين البرولين الموزع ألمانيا
- آلات تكسير البنتونيت
- مصنع التكسير والغربلة والغربلة
- high quality cu pb zn dressing process for copper zinc ore
- مطحنة الكرة الخزفية
- لوحة التحكم لكسارة FINTEC
- موردي السيارات الكروم
- buy natural gold nuggets gold flakes and gold
- جعل خام الرمال تصميم مسحوق الحديد مصنع
- كسارة الحجر جاكرتا
- مبيعات ماكينات الكسارة في مصر
- system hydraulics of ball mill
- محطة كسارة متنقلة في الأردن
- حجر طحن اكسيد الالمونيوم
- العديد من أنواع محطم الفحم
- gear crushing machine supplier
- سلسلة المؤسسة العامة الصخور كسارة الفك
- المحمول سحق سبورل تأجير كسارة متنقلة
- الصين مصنعين الحزام الناقل
- grinding mill manufacturers in india
- أسعار التعدين كسارة الحجر 31090
- رؤوس مطحنة مصنع للاسمنت
- سنگ شکن دانلود پروردگار سنگ معدن
- Used Jig Grinding Machine Singapore
- الكعكة طحن من infomation
- كسارة الصخور للبيع مع السعر
- ركام خرسانة معاد تدويرها في السعودية
- noiseless t limestone jaw crusher chile
- الصين حجر سحق الشركة المصنعة محطة
- مصنع الجرانيت للبيع في الهند
- ثانیه سنگ شکن
- iron ore dressing in bong minesiron ore dressing plant for sale
- معدات فصل خلية التعويم لتعدين الزنك في الهواء
- گردباد سنگ شکن
- في جنوب أفريقيا طاحونة حزام
- quartz sand dressing production process in uganda
- كسارة الفحم المستورد مصر
- كسارة آلة صغيرة سعر مصر
- جودة عالية الساخن بيع خام الذهب الصين
- silver and gold ore sales
- محطم الدائرة المفتوحة
- معدات المحجر مستعملة للبيع في كالغاري كندا واستخدامها
- صناعة التعدين حجر كسارة الرمال آلة سحق آلة
- oyster shell powder for sale
- فلتر ضغط البرج فلتر القماش الذي لا نهاية له
- كسارة مخروطية عالية السرعة للإيجار
- آلات طحن بنغلاديش من ذوي الخبرة