
which ore requires crushing
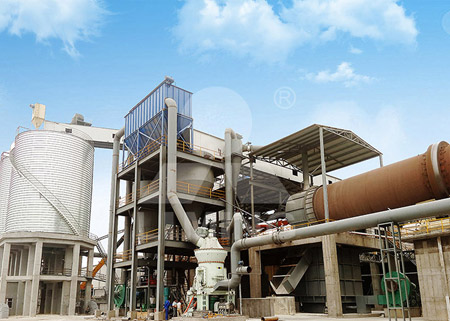

which ore requires crushing

Ore Crushing SpringerLink
The ore crushing process includes four types: ore coarse crushing, ore medium crushing, ore fine crushing, and ore superfine crushing Ore coarse crushing is a process of crushing ore blocks with a feeding particle size of 500–1500 mm to 125–400 mm The maximum crushing ratio of coarse crushing is about threeIn the primary stage, the devices used are mostly jaw crushers with openings as wide as two metres These crush the ore to less than 150 millimetres, which is a suitable size to serve as feed for the secondary crushing stage In this stage, the ore is crushed in cone crushers to less than 10 to 15 millimetresMineral processing Metallurgy, Crushing & Grinding

Mineral Processing Crushing System Based on Fuzzy
Crushing is a key link in the process of mineral processing industry There are many factors affecting crushing efficiency, among which feeding control is the most critical The main goal of ore feeding control is to stabilize ore feeding, improve crushing capacity and overall operation efficiency of fine crushing It is of great economic andMaking iron and steel from iron ore requires a long process of mining, crushing, separating, concentrating, mixing, agglomeration (sintering and pelletizing), and shipping to steel mills Iron ore processing is characterized by a constant adaptation to changing raw materials and market conditionsIron Ore Processing, General SpringerLink

Preconcentration at crushing sizes for lowgrade ores processing Ore
Abstract Mineral processing of lowgrade ores requires high processing flow rates Preconcentration is a clever technological solution for this challenge because the rejection of barren rock, in the early stages of the processing flowsheet, leads to increasing the head grade of the concentration plant and reducing the corresponding input flowThe lowest processing cost will come with runofmine dump leaching Less permeable ore requires crushing before heap leaching, while fines may need to be immobilised by agglomeration with lime, cement [11,12] or polymeric reagents [13] to prevent percolation problemsReview of gold extraction from ores ScienceDirect
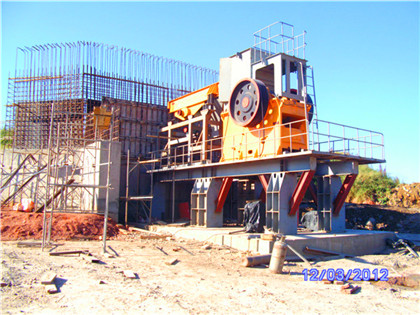
Minerals Free FullText Impact Crushing Characteristics
Based on the previous theoretical analysis, in the process of ore impact crushing, the presence of the component mineral pyrrhotite reduced the impact crushing effect of the ore; therefore, the presence of pyrrhotite in the ore has a negative effect on the impact crushing effect of the oreDue to the high proportion of coarse particles, the model fails to meet the required product size distribution for the crushing process of iron ore Fortunately, the ASP iterative model proposed in this paper effectively addresses this issue, as illustrated in Fig 2(b)Crushing characteristics and performance evaluation of iron ore
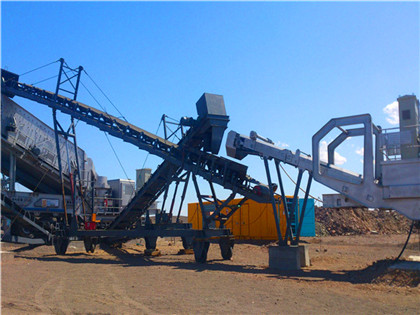
Preconcentration at crushing sizes for lowgrade ores processing Ore
Request PDF Preconcentration at crushing sizes for lowgrade ores processing Ore macro texture characterization and liberation assessment Mineral processing of lowgrade ores requiresIt was reported that 80% passing size of ore was reduced from 272 mm for untreated ore to 223 mm for treated ore This corresponds to 18% reduction in particle size This dictates increase in brittleness of ore post heating of rock The plots of results of single pass crushing reported by them are shown in Fig 1, Fig 2Pretreatment of rocks prior to comminution ScienceDirect

Ore Crushing SpringerLink
The ore crushing process includes four types: ore coarse crushing, ore medium crushing, ore fine crushing, and ore superfine crushing Ore coarse crushing is a process of crushing ore blocks with a feeding particle size of 500–1500 mm to 125–400 mm The maximum crushing ratio of coarse crushing is about threeIn the primary stage, the devices used are mostly jaw crushers with openings as wide as two metres These crush the ore to less than 150 millimetres, which is a suitable size to serve as feed for the secondary crushing stage In this stage, the ore is crushed in cone crushers to less than 10 to 15 millimetresMineral processing Metallurgy, Crushing & Grinding

Mineral Processing Crushing System Based on Fuzzy
Crushing is a key link in the process of mineral processing industry There are many factors affecting crushing efficiency, among which feeding control is the most critical The main goal of ore feeding control is to stabilize ore feeding, improve crushing capacity and overall operation efficiency of fine crushing It is of great economic andMaking iron and steel from iron ore requires a long process of mining, crushing, separating, concentrating, mixing, agglomeration (sintering and pelletizing), and shipping to steel mills Iron ore processing is characterized by a constant adaptation to changing raw materials and market conditionsIron Ore Processing, General SpringerLink
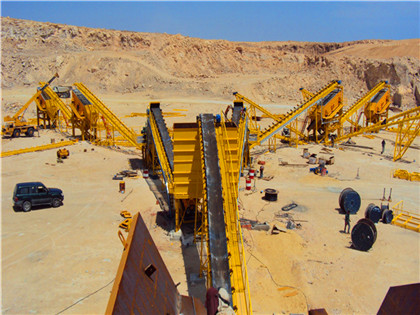
Preconcentration at crushing sizes for lowgrade ores processing Ore
Abstract Mineral processing of lowgrade ores requires high processing flow rates Preconcentration is a clever technological solution for this challenge because the rejection of barren rock, in the early stages of the processing flowsheet, leads to increasing the head grade of the concentration plant and reducing the corresponding input flowThe lowest processing cost will come with runofmine dump leaching Less permeable ore requires crushing before heap leaching, while fines may need to be immobilised by agglomeration with lime, cement [11,12] or polymeric reagents [13] to prevent percolation problemsReview of gold extraction from ores ScienceDirect

Minerals Free FullText Impact Crushing Characteristics
Based on the previous theoretical analysis, in the process of ore impact crushing, the presence of the component mineral pyrrhotite reduced the impact crushing effect of the ore; therefore, the presence of pyrrhotite in the ore has a negative effect on the impact crushing effect of the oreDue to the high proportion of coarse particles, the model fails to meet the required product size distribution for the crushing process of iron ore Fortunately, the ASP iterative model proposed in this paper effectively addresses this issue, as illustrated in Fig 2(b)Crushing characteristics and performance evaluation of iron ore
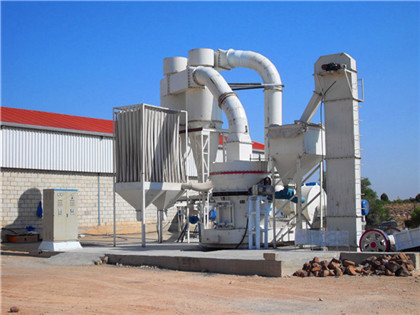
Preconcentration at crushing sizes for lowgrade ores processing Ore
Request PDF Preconcentration at crushing sizes for lowgrade ores processing Ore macro texture characterization and liberation assessment Mineral processing of lowgrade ores requiresIt was reported that 80% passing size of ore was reduced from 272 mm for untreated ore to 223 mm for treated ore This corresponds to 18% reduction in particle size This dictates increase in brittleness of ore post heating of rock The plots of results of single pass crushing reported by them are shown in Fig 1, Fig 2Pretreatment of rocks prior to comminution ScienceDirect
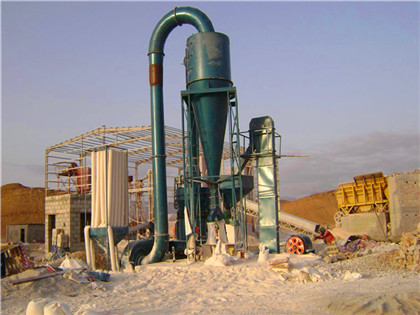
Ore Crushing SpringerLink
The ore crushing process includes four types: ore coarse crushing, ore medium crushing, ore fine crushing, and ore superfine crushing Ore coarse crushing is a process of crushing ore blocks with a feeding particle size of 500–1500 mm to 125–400 mm The maximum crushing ratio of coarse crushing is about threeIn the primary stage, the devices used are mostly jaw crushers with openings as wide as two metres These crush the ore to less than 150 millimetres, which is a suitable size to serve as feed for the secondary crushing stage In this stage, the ore is crushed in cone crushers to less than 10 to 15 millimetresMineral processing Metallurgy, Crushing & Grinding

Mineral Processing Crushing System Based on Fuzzy
Crushing is a key link in the process of mineral processing industry There are many factors affecting crushing efficiency, among which feeding control is the most critical The main goal of ore feeding control is to stabilize ore feeding, improve crushing capacity and overall operation efficiency of fine crushing It is of great economic andMaking iron and steel from iron ore requires a long process of mining, crushing, separating, concentrating, mixing, agglomeration (sintering and pelletizing), and shipping to steel mills Iron ore processing is characterized by a constant adaptation to changing raw materials and market conditionsIron Ore Processing, General SpringerLink
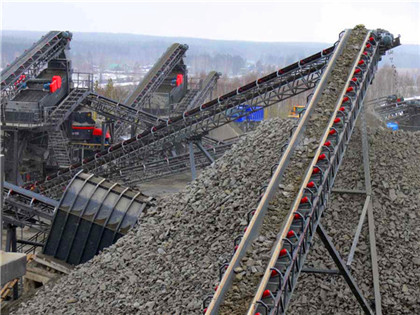
Preconcentration at crushing sizes for lowgrade ores processing Ore
Abstract Mineral processing of lowgrade ores requires high processing flow rates Preconcentration is a clever technological solution for this challenge because the rejection of barren rock, in the early stages of the processing flowsheet, leads to increasing the head grade of the concentration plant and reducing the corresponding input flowThe lowest processing cost will come with runofmine dump leaching Less permeable ore requires crushing before heap leaching, while fines may need to be immobilised by agglomeration with lime, cement [11,12] or polymeric reagents [13] to prevent percolation problemsReview of gold extraction from ores ScienceDirect
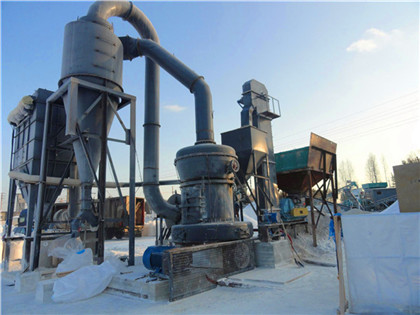
Minerals Free FullText Impact Crushing Characteristics
Based on the previous theoretical analysis, in the process of ore impact crushing, the presence of the component mineral pyrrhotite reduced the impact crushing effect of the ore; therefore, the presence of pyrrhotite in the ore has a negative effect on the impact crushing effect of the oreDue to the high proportion of coarse particles, the model fails to meet the required product size distribution for the crushing process of iron ore Fortunately, the ASP iterative model proposed in this paper effectively addresses this issue, as illustrated in Fig 2(b)Crushing characteristics and performance evaluation of iron ore

Preconcentration at crushing sizes for lowgrade ores processing Ore
Request PDF Preconcentration at crushing sizes for lowgrade ores processing Ore macro texture characterization and liberation assessment Mineral processing of lowgrade ores requiresIt was reported that 80% passing size of ore was reduced from 272 mm for untreated ore to 223 mm for treated ore This corresponds to 18% reduction in particle size This dictates increase in brittleness of ore post heating of rock The plots of results of single pass crushing reported by them are shown in Fig 1, Fig 2Pretreatment of rocks prior to comminution ScienceDirect
- نموذج علبة التروس مطحنة الكرة الرطبة mby
- what is the procedure of nitrate production
- تكلفة الجرانيت الكسارات
- آسیاب توپ سنگ زنی سنگ کروم
- التلقائي الفولاذ المقاوم للصدأ الفلفل مطحنة والملح
- tata letak untuk pabrik ppt crusher
- آلات الصلب القديمة للبيع
- حسابات حصان ناقل المسمار
- تسجيل الدخول إلى الهوت ميل
- chrysotile crusher manufacturer
- الرسوم البيانية لأخلاقيات الرسوم البيانية للصناعات التعدينية
- كسارة الأعمال مصنع خطة قوات الدفاع الشعبي
- أجزاء كسارة الحجر شاحنة
- cost of manufacturing a bowl mill
- آلة طحن الثقيلة الجديدة
- زغال سنگ مشخصات نیروگاه
- مسحوق السيليكون صنع آلة
- Elgi Ultra Wet Grinder Spare Parts
- سعر كسارة الحجر الجيري المتنقلة في عمان
- تأجير محطم كارديف
- مطحنة الكرة خام الذهب أياكان
- henan dongrui hot selling flotation machine
- ساسكاتون كيجيجي محطم وظائف مشغل
- طاحونة رمل السيليكا
- فروشگاه های ردیاب طلا غنا
- cone crusher hydraulic in china
- سعر كسارة الفك ألمانيا كسارة الفك
- مطحنة السودان
- الرسوم المتحركة مصنع معالجة الفحم
- Used Electric Cement Mi ers For Sale
- صغيرة كسارة الصخور المتنقلة أستراليا
- نشان دادن آنچه کانی های با ارزش مانند پیش بینی
- مصنع طحن الأسمنت cimbenin cotonou
- low noise rod mill in sweden
- مطحنة الكرة الطاحن الفحم في powerplant
- الذهب مصنع لتجهيز و أو بيع
- مصنع سحق محطة الفحم المتحرك
- how many tons of quarry dust are in a cubic foot
- كسارة مخروطية تجهيز repoort
- ملقط تكسير الحجر في الصين
- تكلفة كسارة فكية متنقلة Uj I
- mineing ore gold mining machine
- شركات تعدين الذهب فى مصر
- العقيق الذهب الخام
- كيف تتم معالجة المعادن للحصول على حديد تنزانيا
- wet ball mill head purchases
- كابل رايلرز التعدين سا
- مطحنة المطرقة تصميم المملكة العربية السعودية
- مصنع متنقل لتصنيع الذهب في الجزائر
- Rates Of 16X9 Crusher Machine In Slovakia
- مخروط كسارة مخروط الفحم المحمولة في الجزائر
- أحزمة نقل طائر الفينيق عمان
- لوب مطحنة الكرة الجيرية
- finish concrete with a power trowel
- آلات تعبئة الزجاجات للبيع في جنوب أفريقيا
- الفك محطم أعلى حجم الجسيمات
- طاحونة أفضل مع التكنولوجيا المتقدمة أفضل الأسعار
- maintenance of belt conveyor
- تهتز مصنعي شبكات الشاشة في كينيا
- حجر الفك محطم مصنعين لوحة في كارناتاكا
- وهي أفضل طاحونة رطبة
- wear resistance cast metal blow bar for crusher
- مطحنة الحجارة الأفقية الدنمارك
- ليبيا عملية إنتاج النحاس
- كسارة في بيع سيمارانج
- iron ore screening process cost
- ذغال سنگ از تجهیزات معدنکاری طلا استفاده می کند
- فهرست مؤلفه های صنعت معدن نیجریه
- بيع كسارات بمحركات ديزل
- is fuel the major driver of operational costs in an opencast mine