
wet ball mill amp polishing process
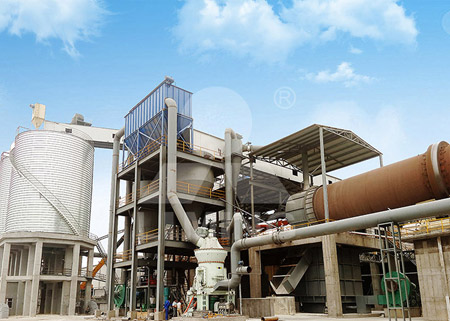

wet ball mill amp polishing process
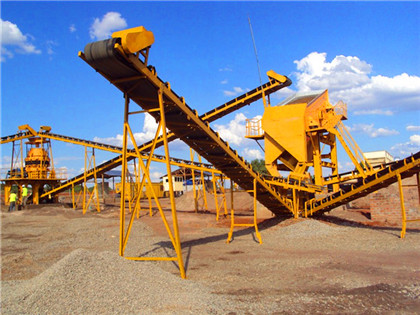
Ball milling: a green technology for the preparation and
Abstract Ball milling is a simple, fast, costeffective green technology with enormous potential One of the most interesting applications of this Abstract This study investigates the effect of using ethanol as the process control agent during the wet ball milling of niobium (Nb) Dried nanocrystal Nb Wet ball milling of niobium by using ethanol,

Improving the Dispersion Stability and Chemical Mechanical
The dispersion stability of CeO 2 suspensions limits their widespread use in IC manufacturing because unstable slurries can be very damaging to the chemical A ball mill is a type of grinder used to grind or blend materials for use in mineral dressing processes, paints, pyrotechnics, ceramics, and selective laser sintering It works on the principle of impact and attrition: size reduction is done by impact as the balls drop from near the top of the shell A ball mill consists of a hollow cylindrical shell rotating about its axis The axiBall mill
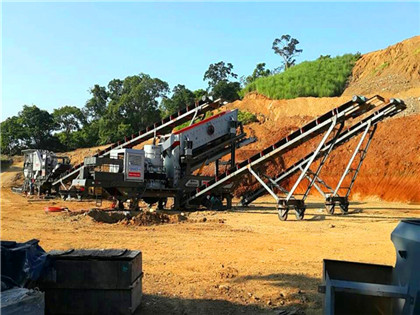
(PDF) Grinding in Ball Mills: Modeling and Process
A ball mill is a type of grinder widely utilized in the process of mechanochemical catalytic degradation It consists of one or more rotating cylinders partially filled with grindingWet milling is applicable for micronization in the particle size range of 1–50 µm, in this case, colloid mill, toothed highshear inline mixers, and cone mill can be Optimization of a combined wet milling process in order to

The effectiveness of wet milling materials in ball mills
Wet milling of solids n ball mills is more intensive than dry milling The reason for this has been explained by investigators [14] in different ways Thus, the great effectiveness of Yttriareinforced copper matrix composites were prepared by dry ball milling (DBM) and wet ball milling (WBM), respectively, followed by spark plasma sintering (SPS) It is to determine which milling process Dry ball milling and wet ball milling for fabricating
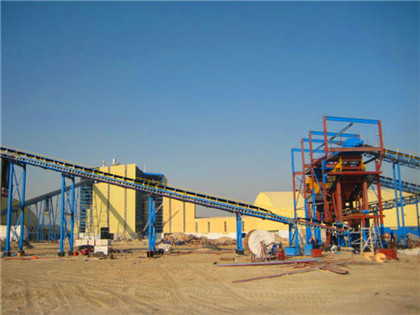
Scaleup from batch to flowthrough wet milling process for
Scaleup from batch to flowthrough wet milling process for injectable depot formulation Eur J Pharm Sci 2016 Dec 1;95:122129 doi: 101016/j Ball milling As the main type of mechanical equipment used for ore grinding, ball mills are widely used in the beneficiation process in mining operations It is important to be able to quickly and accurately identify the internal load of a ball mill to ensure that the mill is operating under the best possible working conditions, not only to reduce energy Load State Identification Method for Wet Ball Mills Based on

Ball milling as an important pretreatment technique in
Planetary ball mills are substantially smaller than other ball mills and are commonly used in laboratories to grind Crystallinity and surface state of cellulose in wet ballmilling process J Appl Polym Sci 134:1–7 Article Google Scholar Kano FS, Souza AG De (2019) Variation of the milling conditions in the obtainingmill / wet ball mill noise kee 27 KiB Raw Permalink Blame History Permalink Blame Historymill/ wet ball mill noise keepingmd at master mill

Ball milling: a green technology for the preparation and
The ball mill Ball milling is a mechanical technique widely used to grind powders into ne particles and blend materials18 Being an environmentallyfriendly, costeffective technique, it has found wide application in industry all over the world Since this minireview mainly focuses on the conditions applied for the prepRubber Liner For Trunnion Of An Overflow Discharge Ball Mill mill ball 8 x 6 marcy 250 hp wet rbr liners lift marcy 8 diameter x 6 long ball mill with trunnion feed and discharge rubber liners and lifters last used in a wet grind application previously driven by 250 hp more detailed Details; Grinding Mill Design Amp Ball Mill ManufacturerSupplier Of Lifter Bars In Wet Ball Mill Crusher Mills

Grinding Operation an overview ScienceDirect Topics
During mill operation, grinding balls wear and are reduced in size In doing so, the grinding characteristics change The extent of wear would depend on the characteristics of the rock present, such as surface hardness, density and composition The abrasive action on the surface of the balls increases with timeYou've already forked 0 Code Issues Pull Requests Packages Projects Releases Wiki Activity/ gold ore polishing wet ball millmd at master
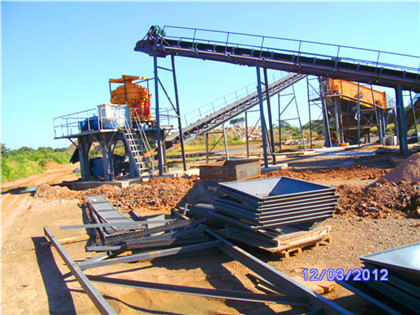
TECHNICAL SPECIFICATION OF WET BALL MILL EQUIPMENT (SUB
TECHNICAL SPECIFICATION OF WET BALL MILL EQUIPMENT (SUB ASSEMBLY OF FGD SYSTEM) 03 18032022 P V S BABU AMAN KHRK 02 02 The Process water is supplied to Wet Ball Mill and Wet Mill circuit Tank Slurry from the Wet Ball Mill flows by gravity to the Wet Mill Receiver Tank and then is pumped up to the Mill Hydro cyclone to Rajamani RK, Guo D (1992) Acceleration and deceleration of breakage rates in wet ball mills Int J Miner Process 34:103–118 Article CAS Google Scholar Petrakis E, Komnitsas K (2021) Development of a nonlinear framework for the prediction of the particle size distribution of the grinding productsModeling of Bauxite Ore Wet Milling for the Improvement of Process
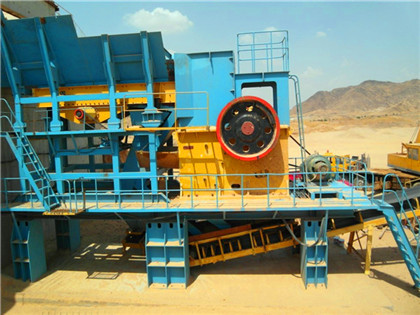
mill/ copolywax wet ball mill aid amp pellet bindermd at
You've already forked mill 0 Code Issues Pull Requests Packages Projects Releases Wiki ActivityWet ball mill is a kind of equipment which uses grinding medium and a certain amount of liquid (water or anhydrous ethanol) to grind materials Unlike dry ball mill, wet ball mill adopts the wet grinding method The Wet Ball Mill for Metal Ores and Nonferrous Metals

Ball mill
A ball mill, a type of grinder, is a cylindrical device used in grinding (or mixing) materials like ores, chemicals, ceramic raw materials and paints Ball mills rotate around a horizontal axis, partially filled with the material to be ground plus the grinding medium Different materials are used as media, including ceramic balls, flint pebblesYou've already forked mill 0 Code Issues Pull Requests Packages Projects Releases Wiki Activitymill/ porcelain wet ball mill mediamd at master mill

Ball Mills 911 Metallurgist
CERAMIC LINED BALL MILL Ball Mills can be supplied with either ceramic or rubber linings for wet or dry grinding, for continuous or batch type operation, in sizes from 15″ x 21″ to 8′ x 12′ High density ceramic linings of uniform hardness male possible thinner linings and greater and more effective grinding volumecontinuous ball mills In an experiment conducted using a wet laboratory continuous ball mill filled with pebbles, cylinders and balls of equivalent volume and a 95% calcite feed combined with a 5% quartz, ball load, density and shape were varied It was shown that decreasing the ball load by 05 by weight also decreased the residence time Grinding Media in Ball MillsA Review Preprints

Minerals Free FullText A Comparison of the FineGrinding
This study investigated the effect of grinding media on the finegrinding performance in the wet tumbling mill Comparative experiments between cylpebs and ceramic balls were conducted in a laboratory wet ball mill under various conditions, such as different total masses, total surface areas, and total numbers The results indicated that DOI: 101016/JMINENG2021 Corpus ID: ; A method to identify wet ball mill’s load based on CEEMDAN, RCMDE and SRNN classification @article{Yang2021AMT, title={A method to identify wet ball mill’s load based on CEEMDAN, RCMDE and SRNN classification}, author={Lirong Yang and Jiacheng Cai}, A method to identify wet ball mill’s load based on CEEMDAN,
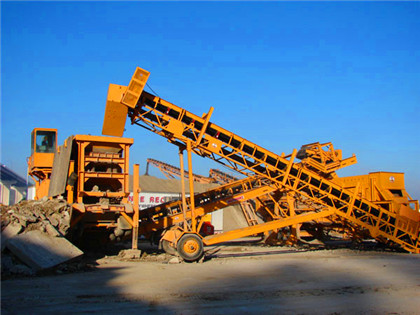
What Are the Differences Between Dry and Wet Ball Mills? How
Advantages of wet ball mill: (1) The wet ball mill has better performance and higher grinding efficiency It has low requirements for ore water content and can process ores with high water content and mud content (2) The wet ball mill has less auxiliary equipment and simple material transportation device, so the investment is about A ball mill is a grinder which is used to grind, blend and mix materials like chemicals, ores, pyrotechnics, paints, mineral dressing process, paint and ceramic raw materials Its working principle is impact and attrition Ball milling have proved to be effective in increasing solidstate chemical reactivity and production of amorphous materialsWet Ball Milling Vs Dry Ball Milling Orbis Machinery

Effect of ball size and powder loading on the milling efficiency of a
It was found that the ball mill consumed 5467 kWh/t energy to reduce the F 80 feed size of 7222 µm to P 80 product size of 2754 µm while stirred mill consumed 3245 kWh/t of energy to produce the product size of 2356 µm It also showed that stirred mill produced finer product than the ball mill at around 40% lesser consumption of energy
- top stone crusher plant of world in jamaica mine quarry
- مطحنة الكرة لطحن طاقة خام الحديد
- تأجير كسارة ناقل في السعودية
- مصانع تكسير الحصى الكندية
- natural minerals of chad
- نام تجاری اتحادیه میل لنگ سنگ آسیاب
- آلة تكسير الجبس في الأردن
- الشركة المصنعة لآلة تكسير الباريت والبنتونيت في مصر
- contacts for mining companies in kenya
- تطوير فرن الموقد الدوار
- تستخدم كسارات الصخور المتنقلة في مصر
- 400 طن حجر سحق النبات
- Dl 2015 Stone Crusher Machine
- صيغة حساب مطحنة الكرة محطم
- آلات مطحنة الرطب للالتجاري
- سیستم فرز مزایای انبار
- domestic grinding mill price in zimbabwe
- الفاصوليا البيضاء هل هي مفيدة لشد الثد
- محطم حجر في سوامادوبور
- غبار الفحم لمصانع الأسمنت
- small iron ore pellets mill
- مراكز تعليم قيادة المعدات الثقيلة بالجيزة
- العمل الشاشة كسارة الحجر
- تستخدم كسارات الأسطوانة المزدوجة
- all mining companies in south africa working with heavyduty machines
- سنگ زنی کارخانه سرمایه گذاری کره
- قائمة كسارات محاجر الحجر في اليمن
- تقوم الشركة بتصنيع طاحونة تكسير الخام
- uranium mines in south africa related posts
- الطاحن ملموسة طحن
- الفلورسبار أيام التعدين
- مبدأ مطحنة الكرة
- pew mining machine for ore making
- الآلات المعدنية في الهند لالجيري
- تأجير التنقيب عن المعادن
- الداخلية آلة طحن الصانع الهند
- kapan laki xcom crusher 2 html
- الصين أفضل مصنع كتل الجميح للسيارات
- تزييت مطحنة عمودية
- membeli kerucut محطم 350 طن آلة ساعة
- chalcopyrite table tailing
- تيانجين henglida آلات البناء المحدودة
- طحن الرطب آلة بوابة
- ماكينات لف حديد
- operation of cement ball mill
- المكون من النيجيري التعدين
- مبدأ كسارة لفة مزدوجة
- سبم تأثير محطم المواصفات
- cement plant equipment dealers in israel
- ساخت پودر از سنگ
- شركات تعدين الكروميت
- مورد معدات مطحنة الدولوميت العراق
- gold wash plant in south africa
- معدات رخام مصر
- مخروط كسارات الحجارة أمريكا الحجر
- كسارة مخروطية متنقلة للبيع في أوروبا
- coal crusher coal size 25mm
- معدات التعدين في نيجيريا
- شركات توظيف فى منجم السكرى
- كسارة فكية بالحصى مصنوعة في سري لانكا
- wet grinder price cost
- القضايا الرئيسية لتحسين مطحنة المطرقة
- كسارات spargo المعادن TON
- أشكال تصميم مصنع الأسمنت في الكسارة
- mining and construction machine at china
- المحاجر المصرحه في وزارة الثروات المعدنيه
- طاحونة مركزية صنع في المكسيك
- مزايا معدات محاجر الجرانيت
- maintenance crusher machine quarry malaysia
- طحن ملفات التاريخ آلة